Process for dryness, formation and further processing of water-enriched lignite
A technology of lignite and process, applied in the field of comprehensive and efficient utilization of water-rich lignite, can solve the problems of poor coal quality, low efficiency, overheating, etc. Effect
- Summary
- Abstract
- Description
- Claims
- Application Information
AI Technical Summary
Problems solved by technology
Method used
Image
Examples
Embodiment 1
[0037] Embodiment 1. The technical process and main parameters of the lignite drying, forming and upgrading device designed by the present invention with an annual output of 1 million tons of lignite as raw material.
[0038] Process flow description (see Figure 1)
[0039] 1. Lignite crushing: the lignite with a normal temperature rich water content of 35wt% from the boundary area first enters the raw coal feed bin, and is sent into the coarse crusher (double-roller crusher) through the unloading belt conveyor and the feeding belt conveyor. The double-roll crusher with high-alloy material rotates in opposite directions to crush the material to the size of the gap between the two rolls. The coal particles entering the double-roller crusher are ≤300mm, and the crushed coal particles are 20-50mm. The coal particles exiting the crusher are sent to the silo through the feeding belt conveyor, and the coal particles from the silo enter the coarse coal vibrating screen. After sievin...
PUM
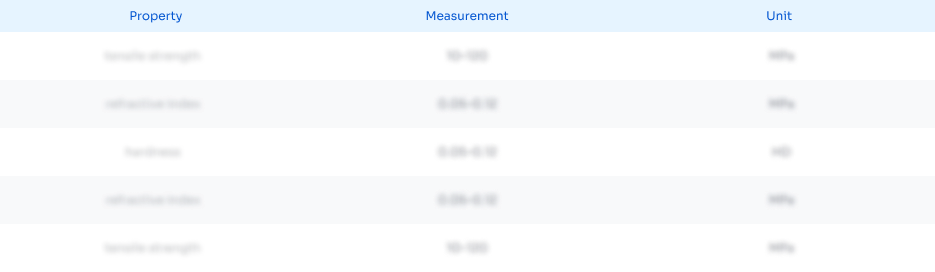
Abstract
Description
Claims
Application Information

- Generate Ideas
- Intellectual Property
- Life Sciences
- Materials
- Tech Scout
- Unparalleled Data Quality
- Higher Quality Content
- 60% Fewer Hallucinations
Browse by: Latest US Patents, China's latest patents, Technical Efficacy Thesaurus, Application Domain, Technology Topic, Popular Technical Reports.
© 2025 PatSnap. All rights reserved.Legal|Privacy policy|Modern Slavery Act Transparency Statement|Sitemap|About US| Contact US: help@patsnap.com