Sintered power generation by waste heat system with by-product gas afterburning
A technology of waste heat power generation and by-product gas, which is applied in waste heat treatment, machines/engines, lighting and heating equipment, etc. It can solve the problems of not increasing the exhaust gas temperature as much as possible, low superheated steam parameters, and low thermal efficiency of the system, so as to increase supplementary combustion The effect of flue gas volume, increasing steam parameters and increasing flue gas temperature
- Summary
- Abstract
- Description
- Claims
- Application Information
AI Technical Summary
Problems solved by technology
Method used
Image
Examples
Embodiment 1
[0013] The structure of this embodiment is as figure 2 As shown, the sintering waste heat power generation system with by-product gas supplementary combustion includes cooler 1, waste heat boiler 16, steam drum 8, steam turbine 9, generator 10, condenser 11, cooling tower 12, condensate water pump 13, oxygen removal 14 and boiler feed water pump 15, the cooler 1 is provided with three exhaust gas outlets, namely the high-temperature exhaust gas outlet 23 located in the high-temperature area, the medium-temperature exhaust gas outlet 22 located in the medium-temperature area, and the low-temperature exhaust gas outlet 21 located in the low-temperature area, and the waste heat boiler 16 Inside from top to bottom, there are a combustion furnace 26, a high-temperature superheater 24, a low-temperature superheater 25, an evaporator 4 and an economizer 5. The combustion furnace 26 of the waste heat boiler 16 is provided with a high-temperature exhaust gas outlet 23, a medium-tempera...
Embodiment 2
[0019] The structure of this embodiment is as image 3 As shown, the difference from Embodiment 1 is that the waste heat boiler 16 is sequentially provided with a combustion furnace 26, a high-pressure superheater 29, a high-pressure evaporator 30, a high-temperature economizer 31, a low-pressure superheater 32, and a low-pressure evaporator. 33 and a low temperature economizer 34, the steam drum is divided into a high pressure drum 35 and a low pressure drum 36, the boiler feed pump 15 is connected to the inlet of the low temperature economizer 34, the outlet of the low temperature economizer 34 is connected to the high temperature economizer 31 The inlet is connected to the water inlet of the low-pressure steam drum 36, the water inlet of the low-pressure evaporator 33 is connected to the water outlet of the low-pressure steam drum 36, the outlet of the low-pressure evaporator 33 is connected to the vapor-liquid two-phase inlet of the low-pressure steam drum 36, and the low-p...
PUM
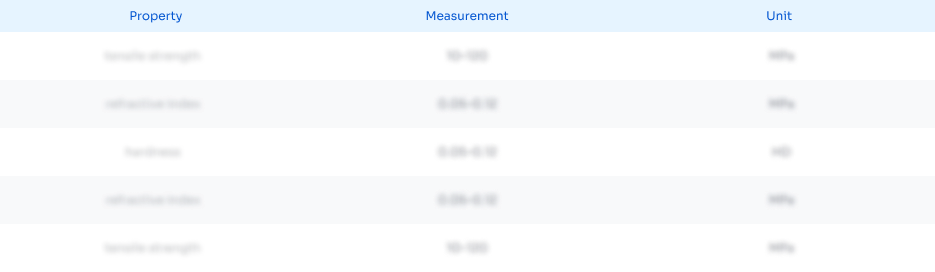
Abstract
Description
Claims
Application Information

- R&D
- Intellectual Property
- Life Sciences
- Materials
- Tech Scout
- Unparalleled Data Quality
- Higher Quality Content
- 60% Fewer Hallucinations
Browse by: Latest US Patents, China's latest patents, Technical Efficacy Thesaurus, Application Domain, Technology Topic, Popular Technical Reports.
© 2025 PatSnap. All rights reserved.Legal|Privacy policy|Modern Slavery Act Transparency Statement|Sitemap|About US| Contact US: help@patsnap.com