Method for producing acid radical-containing polyarylene sulfide resin
一种制造方法、聚芳硫醚的技术,应用在高效率的制造领域,能够解决相容性或密着性的改善效果不充分、分子量低、无法羧基导入等问题
- Summary
- Abstract
- Description
- Claims
- Application Information
AI Technical Summary
Problems solved by technology
Method used
Examples
Embodiment 1
[0107] (Dehydration process: production process of anhydrous sodium sulfide composition)
[0108] In a 1-liter autoclave connected with a pressure gauge, a thermometer, a condenser, a decanter and a zirconium-lined stirring wing, add 220.5 g (1.5 moles) of p-dichlorobenzene (hereinafter abbreviated as p-DCB), 29.7 g (0.3 mol) of NMP, 123.6 g (1.5 mol) of 68 mass % NaSH aqueous solution melted by heating, and 125.0 g (1.5 mol) of 48 mass % NaOH aqueous solution were then stirred under a nitrogen atmosphere at 2 After hours, the temperature was raised to 173° C., and after 123.5 g of water was distilled off, the kettle was sealed. At this time, the DCB distilled off by azeotropy was separated by a decanter and returned to the tank at any time. After the dehydration is completed, the interior of the kettle is in a state where the microparticle-like anhydrous sodium sulfide composition is dispersed in DCB.
[0109] (polymerization process: manufacturing process of PPS)
[0110]...
Embodiment 2
[0114] In the polymerization step, the same operation as in Example 1 was performed except that 0.91 g (0.0045 mol) of 4-chloro-3-nitrobenzoic acid was used instead of 2,4-dichlorobenzoic acid. 156 g of PPS were obtained as a white powder. The melt viscosity of this polymer was 173 Pa·s. The melt viscosity (η') of the composition of this polymer and 3-glycidoxypropyltrimethoxysilane was 805 Pa·s, and the degree of viscosity increase was 4.7 times.
Embodiment 3
[0115] Example 3 (4-dichlorobenzoic acid is introduced into a carboxyl group at the end of the molecule according to the post-addition method)
[0116] In the polymerization process, the same operation as in Example 1 was performed except that 0.86 g (0.0045 mol) of 2,4-dichlorobenzoic acid was heated up to 250° C. and then used in 1 hour. 154 g of PPS were obtained as white powder. The melt viscosity of this polymer was 176 Pa·s. The melt viscosity (η') of the composition of this polymer and 3-glycidoxypropyltrimethoxysilane was 940 Pa·s, and the degree of viscosity increase was 5.3 times. When 1-chloronaphthalene was added to this composition at 0.1% by mass at 285° C., it was completely dissolved, showing that the molecular weight was increased linearly.
PUM
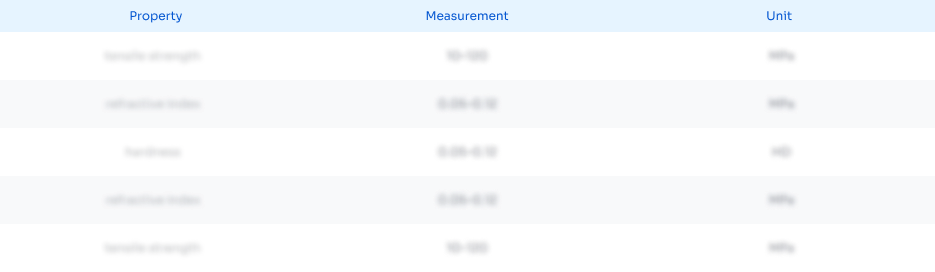
Abstract
Description
Claims
Application Information

- Generate Ideas
- Intellectual Property
- Life Sciences
- Materials
- Tech Scout
- Unparalleled Data Quality
- Higher Quality Content
- 60% Fewer Hallucinations
Browse by: Latest US Patents, China's latest patents, Technical Efficacy Thesaurus, Application Domain, Technology Topic, Popular Technical Reports.
© 2025 PatSnap. All rights reserved.Legal|Privacy policy|Modern Slavery Act Transparency Statement|Sitemap|About US| Contact US: help@patsnap.com