Method for producing oxalic ester with CO coupling
A coupling technology for producing oxalate and coupling, which is applied in the direction of carbon monoxide or formate reaction preparation, organic chemistry, etc., can solve the problems of low selectivity of oxalate and low conversion rate of CO per pass, and achieve high selectivity , catalytic selectivity and activity improvement, and the effect of reducing cycle energy consumption
- Summary
- Abstract
- Description
- Claims
- Application Information
AI Technical Summary
Problems solved by technology
Method used
Examples
Embodiment 1
[0017] CO and methyl nitrite are used as raw materials I, and the molar ratio of CO and methyl nitrite is 1.2:1. The raw materials first enter the coupling reactor and contact with the palladium-containing catalyst, and the reaction generates unreacted nitrous acid containing nitrogen oxides. The reaction effluent I of methyl ester, CO and dimethyl oxalate; after the reaction effluent I is separated by gas and liquid, the liquid phase reaction effluent II and the gas phase reaction effluent III are obtained, and the gas phase reaction effluent III, O 2 and methanol as the raw material II, and the raw material II enters the regeneration reactor for reaction to generate a gas effluent IV containing methyl nitrite, and the gas effluent IV returns to the coupling reactor to continue the reaction; the liquid phase reaction effluent II is obtained after separation Dimethyl oxalate product. Among them, the reaction conditions of the coupling reactor: the reaction temperature is 90°C,...
Embodiment 2
[0019] CO and methyl nitrite are used as raw materials I, and the molar ratio of CO and methyl nitrite is 1:1. The raw materials first enter the coupling reactor and contact with the palladium-containing catalyst, and the reaction generates unreacted nitrous acid containing nitrogen oxides. Reaction effluent I of methyl ester, CO and dimethyl oxalate ester; after gas-liquid separation of reaction effluent I, liquid-phase reaction effluent II and gas-phase reaction effluent III are obtained, and gas-phase reaction effluent III, O 2 and methanol as the raw material II, and the raw material II enters the regeneration reactor for reaction to generate a gas effluent IV containing methyl nitrite, and the gas effluent IV returns to the coupling reactor to continue the reaction; the liquid phase reaction effluent II is obtained after separation Dimethyl oxalate product. Among them, the reaction conditions of the coupling reactor: the reaction temperature is 120°C, the reaction contact...
Embodiment 3
[0021] CO and ethyl nitrite are used as raw materials I, and the molar ratio of CO and ethyl nitrite is 3:1. The raw materials first enter the coupling reactor and contact with the palladium-containing catalyst, and the reaction generates unreacted nitrous acid containing nitrogen oxides. The reaction effluent I of ethyl ester, CO and diethyl oxalate; after the reaction effluent I is separated by gas and liquid, the liquid phase reaction effluent II and the gas phase reaction effluent III are obtained, and the gas phase reaction effluent III, O 2 and ethanol as the raw material II, the raw material II enters the regeneration reactor for reaction, and generates a gas effluent IV containing ethyl nitrite, and the gas effluent IV returns to the coupling reactor to continue the reaction; the liquid phase reaction effluent II is obtained after separation Diethyl oxalate product. Among them, the reaction conditions of the coupling reactor: the reaction temperature is 130 ° C, the re...
PUM
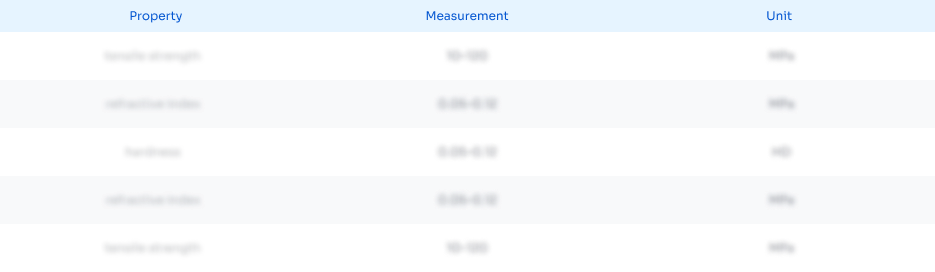
Abstract
Description
Claims
Application Information

- Generate Ideas
- Intellectual Property
- Life Sciences
- Materials
- Tech Scout
- Unparalleled Data Quality
- Higher Quality Content
- 60% Fewer Hallucinations
Browse by: Latest US Patents, China's latest patents, Technical Efficacy Thesaurus, Application Domain, Technology Topic, Popular Technical Reports.
© 2025 PatSnap. All rights reserved.Legal|Privacy policy|Modern Slavery Act Transparency Statement|Sitemap|About US| Contact US: help@patsnap.com