Non-molybdenum non-nickel middle chrome wear resistant steel casting and heat treatment method thereof
A heat treatment method and steel casting technology are applied in the field of metal wear-resistant materials, which can solve the problem of high production cost and achieve the effects of good hardness uniformity, high hardness and low production cost
- Summary
- Abstract
- Description
- Claims
- Application Information
AI Technical Summary
Problems solved by technology
Method used
Image
Examples
Embodiment 1
[0059] The steps of the heat treatment method for smelting the non-molybdenum-nickel medium-chromium wear-resistant steel castings provided by the present invention with a 500 kg intermediate frequency induction electric furnace are:
[0060] ① Heat and melt scrap steel, pig iron, ferrochrome, ferrosilicon and ferromanganese;
[0061] ②After adjusting the composition in front of the furnace, the temperature is raised to 1592℃, pre-deoxidized with silicon-calcium alloy, and finally deoxidized with aluminum, and then out of the furnace. The percentage of silicon-calcium alloy added to the mass of molten steel is 0.28%, and the amount of aluminum added to molten steel is 0.28%. The mass percentage is 0.11%;
[0062] ③Crush the yttrium-based rare earth, titanium-iron, boron-iron, and vanadium-nitrogen alloys into small pieces with a particle size of less than 12mm, dry them below 220 ℃, place them at the bottom of the ladle, and use the ladle flushing method to perform compound modifi...
Embodiment 2
[0071] The steps of the heat treatment method for smelting the molybdenum-nickel-free medium-chromium wear-resistant cast steel provided by the present invention in a 1000 kg intermediate frequency induction electric furnace are:
[0072] ① Heat and melt scrap steel, pig iron, ferrochrome, ferrosilicon and ferromanganese;
[0073] ② Adjust the composition in front of the furnace and raise the temperature to 1619℃, pre-deoxidize with silicon-calcium alloy, and finally deoxidize with aluminum, and then out of the furnace. The percentage of silicon-calcium alloy added to molten steel mass is 0.18%. The mass percentage is 0.15%;
[0074] ③Crush the yttrium-based rare earth, titanium-iron, boron-iron, and vanadium-nitrogen alloys into small pieces with a particle size of less than 12mm, dry them below 220 ℃, place them at the bottom of the ladle, and use the ladle flushing method to perform compound modification treatment on the molten steel ;
[0075] ④The casting is made of sand cast...
Embodiment 3
[0084] The 750 kg intermediate frequency induction electric furnace is used to melt the molybdenum-nickel-free medium-chromium wear-resistant steel castings provided by the present invention, and the heat treatment steps are as follows:
[0085] ① Heating and melting scrap steel, pig iron, ferrochrome, ferrosilicon and ferromanganese;
[0086] ② Adjust the composition in front of the furnace and raise the temperature to 1604℃, pre-deoxidize with silicon-calcium alloy, and finally deoxidize with aluminum, and then come out of the furnace. The percentage of silicon-calcium alloy added to the mass of molten steel is 0.22%, and the added amount of aluminum is compared with molten steel. The mass percentage is 0.13%;
[0087] ③Crush the yttrium-based rare earth, titanium-iron, boron-iron, and vanadium-nitrogen alloys into small pieces with a particle size of less than 12mm, dry them below 220 ℃, place them at the bottom of the ladle, and use the ladle flushing method to perform compoun...
PUM
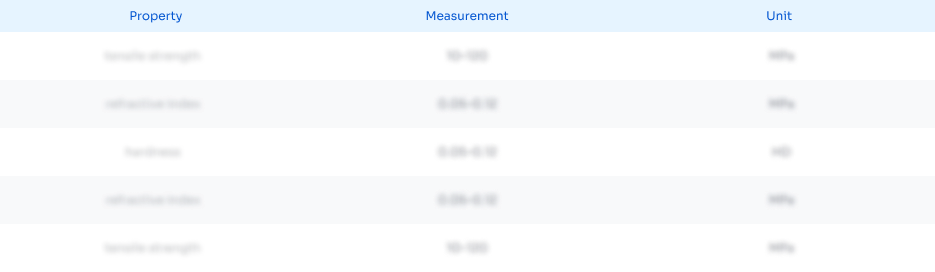
Abstract
Description
Claims
Application Information

- Generate Ideas
- Intellectual Property
- Life Sciences
- Materials
- Tech Scout
- Unparalleled Data Quality
- Higher Quality Content
- 60% Fewer Hallucinations
Browse by: Latest US Patents, China's latest patents, Technical Efficacy Thesaurus, Application Domain, Technology Topic, Popular Technical Reports.
© 2025 PatSnap. All rights reserved.Legal|Privacy policy|Modern Slavery Act Transparency Statement|Sitemap|About US| Contact US: help@patsnap.com