Method for producing rare-earth poly-ferric aluminum silicate sulfate from rare earth-containing sludge and iron-containing dust sludge
A technology of rare earth sulfate and iron dust sludge, which is applied in the direction of flocculation/precipitation water/sewage treatment, etc., can solve the problems of expensive chemical raw materials, low effective concentration, poor stability, etc., to reduce production costs and sewage treatment costs, Excellent performance and good product stability
- Summary
- Abstract
- Description
- Claims
- Application Information
AI Technical Summary
Problems solved by technology
Method used
Image
Examples
example 1
[0022] (1). Weigh 2 kg of rare earth-containing sludge and 3.6 kg of steelmaking dust and mix them thoroughly, and put the rare earth-containing sludge and steelmaking dust into an acid-resistant reaction kettle at a weight percentage of 1:1.8.
[0023] (2). 52L mass percent concentration 10% H2SO4 is slowly poured into the reactor to carry out acid hydrolysis to rare earth sludge and steelmaking dust sludge, containing rare earth sludge, steelmaking dust sludge: 10%H2SO4 by weight 1 : 10 and fully stirred for 1 hour, the reaction system was cooled to room temperature, and the acidolysis reaction was completed.
[0024] (3). Filter the reaction product to remove the precipitate (mainly gypsum and acid insoluble matter), and the filtrate (mainly a mixed solution of ferrous salt, ferric salt, aluminum salt, lanthanum salt, cerium salt and hydrated silicic acid) Use 27.5% H2O2 to make all Fe2+ in the solution be oxidized to Fe3+, and the oxidation end point of the process of oxid...
example 2
[0026] (1). Weigh 2 kg of rare earth-containing sludge and 4 kg of steelmaking dust and mix them thoroughly, and put the rare earth-containing sludge and steelmaking dust into the acid-resistant reaction kettle at a weight percentage of 1:2.
[0027] (2). 99L mass percent concentration 5% H2SO4 is slowly poured into the reactor to carry out acid hydrolysis to rare earth sludge and steelmaking dust sludge, and rare earth sludge, steelmaking dust sludge: 5% H2SO4 by weight 1 : 17 was fully stirred for 1 hour, and the reaction system was cooled to room temperature, and the acidolysis reaction was completed.
[0028] (3). Filter the reaction product to remove the precipitate (mainly gypsum and acid insoluble matter), and the filtrate (mainly a mixed solution of ferrous salt, ferric salt, aluminum salt, lanthanum salt, cerium salt and hydrated silicic acid) Use 27.5% H2O2 to make all Fe2+ in the solution be oxidized to Fe3+, and the oxidation end point of the process of oxidizing F...
PUM
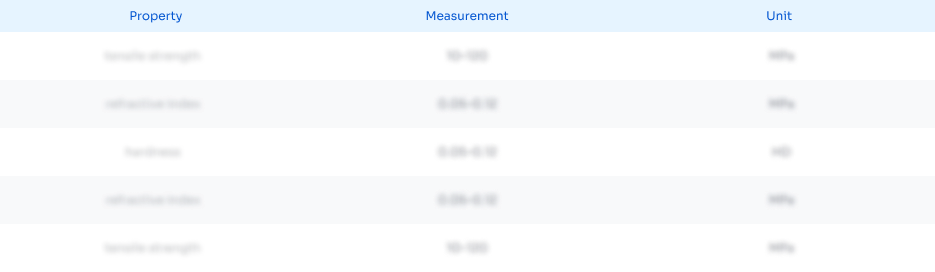
Abstract
Description
Claims
Application Information

- R&D
- Intellectual Property
- Life Sciences
- Materials
- Tech Scout
- Unparalleled Data Quality
- Higher Quality Content
- 60% Fewer Hallucinations
Browse by: Latest US Patents, China's latest patents, Technical Efficacy Thesaurus, Application Domain, Technology Topic, Popular Technical Reports.
© 2025 PatSnap. All rights reserved.Legal|Privacy policy|Modern Slavery Act Transparency Statement|Sitemap|About US| Contact US: help@patsnap.com