Production process for coproduction of iron oxide red and concentrated sulfuric acid
A technology of iron oxide red and production process, applied in the chemical field, can solve problems such as increasing production cost and polluting the environment, and achieve the effects of improving quality, eliminating environmental pollution and reducing production cost
- Summary
- Abstract
- Description
- Claims
- Application Information
AI Technical Summary
Problems solved by technology
Method used
Image
Examples
Embodiment 1
[0019] In the 1000L reaction tank, the first step is pretreatment: first add 400kg of refined iron powder, 40kg of sulfur powder, then mix and stir 40kg of sulfuric acid with a concentration of 90%, and react for 3 hours, and the iron powder and sulfuric acid undergo vulcanization reaction , to generate a mixture of ferric sulfate and ferrous sulfate. When heated to 140°C, keep for 2 to 4 hours for post-treatment and molding, and then send it to the dispersing machine through a belt conveyor to disperse it. After screening, the particle size is 100 mesh and the moisture content is 1. 8% is sent to a Φ3000mm boiling furnace for roasting through a belt conveyor.
[0020] The second step is roasting. Air at normal pressure is blown into the bottom of the fluidized furnace through a blower, and the materials from the raw material section stored in the feeding hopper in front of the furnace are evenly fed into the fluidized furnace through a belt feeder. Sulfur is used as the heat ...
Embodiment 2
[0037] The technical process is the same as that in Example 1, the material proportioning is 400kg fine iron fine powder, 120kg sulfur powder, and then mix in 400kg concentration of 70% sulfuric acid.
Embodiment 3
[0039] The technical process is the same as that in Example 1, the ratio of materials is 400kg of fine iron powder, 60kg of sulfur powder, and then 100kg of sulfuric acid with a concentration of 80%.
PUM
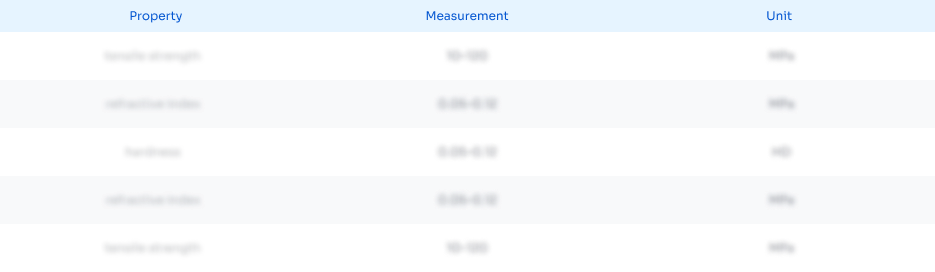
Abstract
Description
Claims
Application Information

- R&D Engineer
- R&D Manager
- IP Professional
- Industry Leading Data Capabilities
- Powerful AI technology
- Patent DNA Extraction
Browse by: Latest US Patents, China's latest patents, Technical Efficacy Thesaurus, Application Domain, Technology Topic, Popular Technical Reports.
© 2024 PatSnap. All rights reserved.Legal|Privacy policy|Modern Slavery Act Transparency Statement|Sitemap|About US| Contact US: help@patsnap.com