Method for producing high quality triarylphosphate
A technology of a triaryl phosphate ester and a production method, which is applied in chemical instruments and methods, compounds of Group 5/15 elements of the periodic table, organic chemistry, etc. Effect
- Summary
- Abstract
- Description
- Claims
- Application Information
AI Technical Summary
Problems solved by technology
Method used
Examples
Embodiment Construction
[0016] Concrete steps of the present invention are as follows:
[0017] a. Alkylation reaction, put 600Kg of melted phenol into a 1000-liter reactor, start stirring, and inject steam into the jacket of the reactor to raise the temperature in the reactor to 115°C, then start to feed propylene Until the mass ratio of phenol to propylene is 1:0.16, the reaction temperature is controlled by the amount of feed in the whole feeding process, the reaction temperature is kept at 115-125 ° C, and the reaction time is 9-10 hours; after that, the deepening reaction is carried out, and the time is 0.5 -1 hour, flush with nitrogen to cool, and keep the temperature at 50-55°C.
[0018] b. Esterification reaction. Inhale the finished material of the alkylation reaction into the esterification reaction kettle, turn on the stirring, turn on the electric heating switch, raise the reaction temperature to 60°C, and start to add phosphorus oxychloride dropwise. The whole dropping process starts wit...
PUM
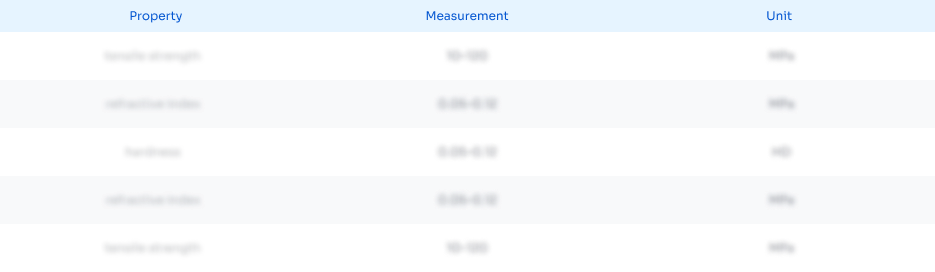
Abstract
Description
Claims
Application Information

- R&D Engineer
- R&D Manager
- IP Professional
- Industry Leading Data Capabilities
- Powerful AI technology
- Patent DNA Extraction
Browse by: Latest US Patents, China's latest patents, Technical Efficacy Thesaurus, Application Domain, Technology Topic, Popular Technical Reports.
© 2024 PatSnap. All rights reserved.Legal|Privacy policy|Modern Slavery Act Transparency Statement|Sitemap|About US| Contact US: help@patsnap.com