Strange-shaped fibre processing technique and spinning jet used in the technique
A special-shaped fiber and processing technology, applied in the direction of fiber type, fiber treatment, fiber chemical characteristics, etc., can solve the problems of unfavorable comfort performance, affecting the abnormality of special-shaped fibers, and affecting fiber quality, etc., to improve friction performance and improve hygroscopic performance. , the effect of good fiber quality
- Summary
- Abstract
- Description
- Claims
- Application Information
AI Technical Summary
Problems solved by technology
Method used
Image
Examples
Embodiment 1
[0028] Such as figure 1 , figure 2 As shown, a spinneret for special-shaped fiber processing has a plurality of spinneret holes 2 distributed on the plate body 1 to form a spinneret hole array, wherein each spinneret hole 2 includes at least two adjacent spray slits 3 ; Wherein, on a section perpendicular to the spinning direction, in each of the spinning holes 2, one side end 5 of each spraying slit 3 is close to each other, and the other side end 5 is far away from each other; In the hole 2, there are four injection slits 3 that are evenly arranged in the circumferential direction, so that the adjacent injection slits 3 are perpendicular to each other on the section perpendicular to the spinning direction.
[0029] In the present embodiment, the processing technology of special-shaped fiber comprises the following steps:
[0030] a. After being heated and pressurized, the polymer melt is sprayed out from the spray slits of the spinneret holes on the spinneret plate;
[0...
Embodiment 2
[0051] Such as image 3 As shown, the difference between this embodiment and Embodiment 1 is that, on the section perpendicular to the spinning direction, the side end 5 of the injection slit 3 is arc-shaped, and the parameters of the processing technology in this embodiment are:
[0052] 1. The concentration of the oil agent is 7%, and the contents of each component in the oil agent are:
[0053] Sorbitan monooleate 550g
[0054] Neopentyl Glycol Laurate Monoester 200g
[0055] Lauroylamine 220g
[0056] Silicate inorganic superfine powder 20g
[0057] Sodium Carboxymethyl Cellulose 10g
[0058] 2. Spinning speed: 3800(m / min);
[0059] 3. Stretch ratio: 1.25;
[0060] 4. Wind speed: 0.50 (m / min);
[0061] 5. Heat setting temperature 160(℃);
[0062] 6. The spinning temperature is 265(°C);
[0063] 7. The degree of fiber irregularity is 69%.
[0064] The shape degree and wicking height of the obtained shaped fibers are shown in Table 1.
Embodiment 3
[0066] Such as Figure 4 As shown, the difference between this embodiment and Embodiment 1 is that, on the section perpendicular to the spinning direction, in each of the spinning holes 2, the center positions of the side ends 5 of the spraying slits 3 that are close to each other A circular center spray hole 4 is provided. During the spinning process, the high polymer melt is ejected from the central nozzle hole 4 at the same time, and the high polymer melt ejected from each injection slit 3 is more conducive to bonding. The parameters of the processing technology described in this embodiment yes:
[0067] 1. The concentration of the oil agent is 7%, and the contents of each component in the oil agent are:
[0068] Polyoxyethylene(6) Sorbitan Glycerate 340g
[0069] Sorbitan Monooleate 290g
[0070] Neopentyl Glycol Laurate Monoester 200g
[0071] Lauroylamine 100g
[0072] Silicate inorganic superfine powder 35g
[0073] Alkyl dimethyl benzyl ammonium bromide 25g
[...
PUM
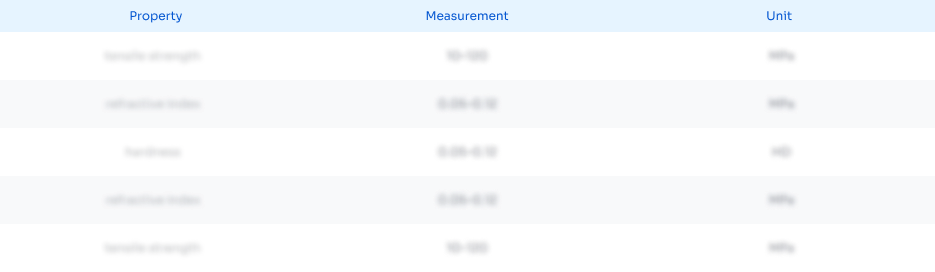
Abstract
Description
Claims
Application Information

- R&D
- Intellectual Property
- Life Sciences
- Materials
- Tech Scout
- Unparalleled Data Quality
- Higher Quality Content
- 60% Fewer Hallucinations
Browse by: Latest US Patents, China's latest patents, Technical Efficacy Thesaurus, Application Domain, Technology Topic, Popular Technical Reports.
© 2025 PatSnap. All rights reserved.Legal|Privacy policy|Modern Slavery Act Transparency Statement|Sitemap|About US| Contact US: help@patsnap.com