Composite grinding aid, production method and uses thereof
A technology of grinding aids and organic aids, applied in the field of composite grinding aids, can solve the problems of cement grinding aids reducing energy consumption in the early and late stages, reducing the early and late strength of cement, and increasing cement water consumption. The effect of reducing unit power consumption, increasing water consumption, and improving compressive strength
- Summary
- Abstract
- Description
- Claims
- Application Information
AI Technical Summary
Problems solved by technology
Method used
Image
Examples
preparation example Construction
[0024] Another embodiment of the present invention provides a kind of preparation method of composite grinding aid, comprises the following steps:
[0025] (1) at least one of polycarboxylic acid and lignin sulfonate, polyhydric fatty alcohol amine, polyhydric fatty alcohol, gluconate that will account for the 1-10% of grinding aid gross weight joins in the reactor, in Stir at room temperature to 100°C for 0.5 to 3 hours to obtain a mixed solution of organic additives for later use;
[0026] (2) at least one of 90-99% sodium silicate and sodium carbonate, sulfate calcined gypsum, and quick lime will be mixed and stirred in a stirrer while the organic compound described in step (1) is The additive mixed solution is evenly sprayed into the agitator, and continuously stirred for 20 to 30 minutes until the mixture is evenly mixed to obtain a composite grinding aid.
[0027] According to another preferred embodiment of the present invention, wherein the polyhydric fatty alcohol am...
Embodiment 1
[0035] Weigh 3g of triethanolamine, 50g of triisopropanolamine, 5g of ethylene glycol, 5g of propylene glycol, 5g of sodium gluconate, and 30g of sodium lignosulfonate, put them into the reaction kettle and stir in turn, and continue stirring when the temperature rises to 80°C After 60 minutes, a uniform mixed solution was prepared for subsequent use. Then weigh 100g of anhydrous sodium sulfate, 600g of calcined gypsum, 50g of quicklime, and 152g of sodium silicate, and put them into the mixer in turn to stir, and at the same time, spray the mixed solution prepared above evenly into the mixer, and continue stirring for 20 minutes to obtain the required Compound grinding aid. The addition weight percentage of this invention product in cement is 0.5%. The cement test results are shown in the table below. It can be seen that the 3-day and 28-day compressive strength increased by 3.1MPa and 5.7MPa respectively, and the water consumption of cement standard consistency decreased b...
Embodiment 2
[0039] Weigh 3g of triethanolamine, 3g of triisopropanolamine, 5g of ethylene glycol, 50g of glycerol, 30g of sodium gluconate, and 9g of polycarboxylic acid, put them into the reaction kettle and stir in turn, and continue stirring when the temperature rises to 95°C After 40 minutes, a uniform mixed solution was prepared for subsequent use. Then take by weighing 150g of anhydrous sodium sulfate, 80g of aluminum sulfate, 170g of calcined gypsum, 300g of quicklime, 200g of sodium carbonate, put into the mixer successively and stir, simultaneously the mixed solution of above-mentioned preparation is evenly sprayed in the mixer, continue to stir again 20 minutes, namely Get the required compound grinding aid. The addition weight percentage of this invention product in cement is 0.5%. The cement test results are shown in the table below. It can be seen that the 3-day and 28-day compressive strength increased by 2.6MPa and 4.3MPa respectively, and the water consumption of cement ...
PUM
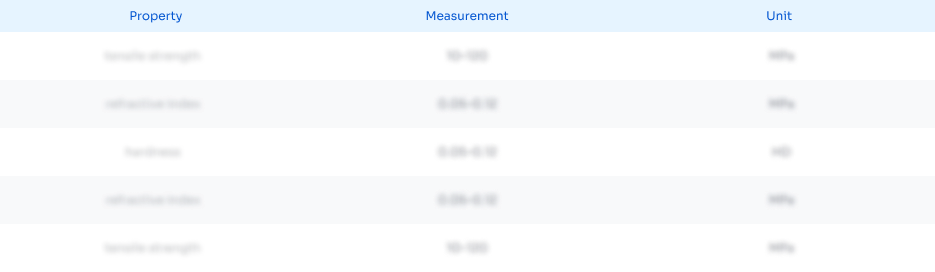
Abstract
Description
Claims
Application Information

- R&D
- Intellectual Property
- Life Sciences
- Materials
- Tech Scout
- Unparalleled Data Quality
- Higher Quality Content
- 60% Fewer Hallucinations
Browse by: Latest US Patents, China's latest patents, Technical Efficacy Thesaurus, Application Domain, Technology Topic, Popular Technical Reports.
© 2025 PatSnap. All rights reserved.Legal|Privacy policy|Modern Slavery Act Transparency Statement|Sitemap|About US| Contact US: help@patsnap.com