Method for preparing Al4SiC4 powder
A powder and system technology, which is applied in the synthesis of refractory materials and ceramics, can solve the problems of complex process, long reaction time and high energy consumption, and achieve the effect of simple preparation process, high ball milling efficiency and low energy consumption
- Summary
- Abstract
- Description
- Claims
- Application Information
AI Technical Summary
Problems solved by technology
Method used
Examples
Embodiment 1
[0015] Metal Al powder (particle size 10 μm, purity ≥ 99%), Si powder (particle size 10 μm, purity ≥ 99%) and carbon black (particle size ≤ 1 μm, purity ≥ 98%, volatile content ≤ 0.2%) in a molar ratio of 4:1 : 4.5 ingredients, dry-mix in polyurethane tank with ball-to-material ratio 3:1 for 3 hours; then take 50 grams of the mixture and put it into the ball mill tank of high-energy ball mill, add aluminum stearate with 0.2% of the mixture mass, put 500 grams For corundum balls, vacuumize to make the vacuum degree less than 1 Pa, pass in argon gas, and ball mill at 800 rpm for 20 hours. Al 4 SiC 4 The purity is more than 80%, and does not contain Al 3 C 4 Mutually.
Embodiment 2
[0017] Metal Al powder (particle size 5 μm, purity ≥ 99%), Si powder (particle size 10 μm, purity ≥ 99%) and carbon black (particle size ≤ 1 μm, purity ≥ 98%, volatile matter ≤ 0.2%) in a molar ratio of 4:1 : 4.2 ingredients, dry mix in a polyurethane tank for 4 hours with a ball-to-material ratio of 3:1; then take 50 grams of the mixture and put it into the ball mill tank of a high-energy ball mill, add aluminum stearate with a weight of 0.3% of the mixture, and put in 600 grams For corundum balls, vacuumize to make the vacuum degree less than 1 Pa, pass in argon gas, and ball mill at 900 rpm for 25 hours. The powder after ball milling was determined to be Al 4 SiC 4 , with a purity of over 84%, and does not contain Al 3 C 4 Mutually.
Embodiment 3
[0019] Metal Al powder (particle size 5 μm, purity ≥ 99%), Si powder (particle size 10 μm, purity ≥ 99%) and graphite (particle size ≤ 1 μm, purity ≥ 98%, volatile content ≤ 0.2%) in a molar ratio of 4:1: 4.2 Ingredients, dry mix in a polyurethane tank with a ball-to-material ratio of 3:1 for 4 hours; then take 50 grams of the mixture and put it into the ball mill tank of a high-energy ball mill, add aluminum stearate with a weight of 0.3% of the mixture, and put 600 grams of corundum The balls are vacuumed to make the vacuum degree less than 1 Pa, and argon gas is introduced, and ball milling is carried out at 1000 rpm for 30 hours. The powder after ball milling was determined to be Al 4 SiC 4 , with a purity of more than 86%, and does not contain Al 3 C 4 Mutually.
PUM
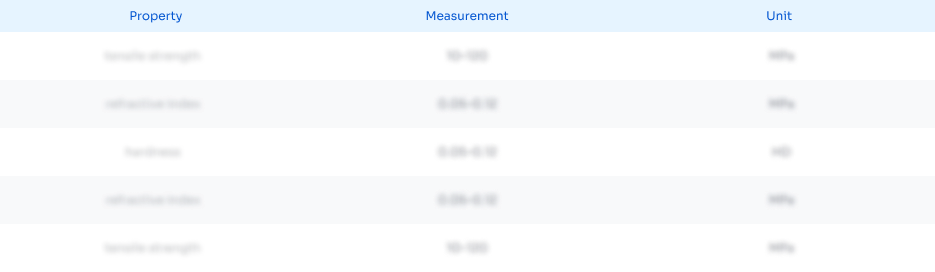
Abstract
Description
Claims
Application Information

- R&D Engineer
- R&D Manager
- IP Professional
- Industry Leading Data Capabilities
- Powerful AI technology
- Patent DNA Extraction
Browse by: Latest US Patents, China's latest patents, Technical Efficacy Thesaurus, Application Domain, Technology Topic, Popular Technical Reports.
© 2024 PatSnap. All rights reserved.Legal|Privacy policy|Modern Slavery Act Transparency Statement|Sitemap|About US| Contact US: help@patsnap.com