Waterborne ultraviolet-heat dual curing coating composite and preparation method thereof
A dual-curing, ultraviolet light technology, applied in the direction of polyurea/polyurethane coatings, coatings, etc., can solve the problems of inapplicability of rapid dual-curing requirements, poor heat resistance, etc., and achieve long pot life, good flexibility, and high hardness. Effect
- Summary
- Abstract
- Description
- Claims
- Application Information
AI Technical Summary
Problems solved by technology
Method used
Image
Examples
Embodiment 1
[0045] Example 1: Add 15.2g of cationic water-based polyurethane acrylate and 20.3g of cationic water-based polyurethane polyol into a 1000ml beaker, stir at 600 rpm for 2 hours, then add 0.87g of photoinitiator Darocur1173 and leveling agent BYK333 0.12g, 0.17g dispersant BYK163, 0.15g defoamer BYK055, 0.05g phosphate adhesion promoter, continue stirring at 600 rpm for 0.5 hours. Finally add 23.5g water-based curing agent (R 8 = Desmodur N3390, m=7), stirred at 800 rpm for 2 minutes, and discharged to obtain a milky white water-based UV-heat dual-curing coating. Among them, R 1 = hydroxyethyl acrylate, R 2 = tolyl, R 3 = polycarbonate diol (molecular weight is 2000), R 4 = methyl, R 5 = Glacial acetic acid, R 7 = ethylene glycol. Spray the prepared paint on the pre-polished, degreased, and derusted tinplate, light-cure it under a 3kw UV lamp for 10 seconds, and then heat-cure it at 60°C for 1 minute. The test results of paint film properties are shown in Table 1.
Embodiment 2
[0046] Example 2: Add 18.1g of anionic water-based polyurethane acrylate and 24.2g of anionic water-based polyurethane polyol into a 1000ml beaker, stir at 600 rpm for 2 hours, then add 1.5g of photoinitiator Darocur184, leveling agent BYK366 0.2g, 0.13g dispersant BYK163, 0.10g defoamer BYK088, 0.07g phosphate adhesion promoter, stirred at 700 rpm for 1.5 hours, and finally added 30.0g water-based curing agent (R 8 = Desmodur N3390, m=2), stirred at 800 rpm for 3 minutes, and discharged to obtain a milky white water-based UV-heat dual-curing coating. Among them, R 1 = hydroxyethyl acrylate, R 2 = tolyl, R 3 = polypropylene glycol (molecular weight is 2000), R 6 = triethylamine, R 7 = ethylene glycol. Spray the prepared paint on the pre-polished, degreased, and derusted tinplate, light-cure it under a 3kw ultraviolet lamp for 30s, and then heat-cure it at 40°C for 3 minutes. The test results of paint film properties are shown in Table 1.
Embodiment 3
[0047] Embodiment 3: 35.0g non-ionic water-based polyurethane acrylate and 41.6g non-ionic water-based polyurethane polyols were added to a 2000ml beaker, stirred at a speed of 800 rpm for 3 hours, then, 0.18g photoinitiator Darocur1173 was added, flow Leveling agent BFKA3883 is 0.22g, 0.15g dispersant BYKP105, 0.12g phosphate adhesion promoter, 800 rev / min speed of stirring for 2 hours, finally add 43.2g water-based curing agent (R 8 = Desmodur R, m=1), stirring at a speed of 900 rpm for 1 minute, and discharging to obtain a milky white water-based UV-heat dual-curing coating. Among them, R 1 = pentaerythritol triacrylate, R 2 = hexamethylene, n = 50, R 7 = Butanediol. Spray the prepared paint on the pre-polished, degreased, and derusted tinplate, light-cure it under a 3kw UV lamp for 20s, and then heat-cure it at 50°C for 3 minutes. The test results of paint film properties are shown in Table 1.
PUM
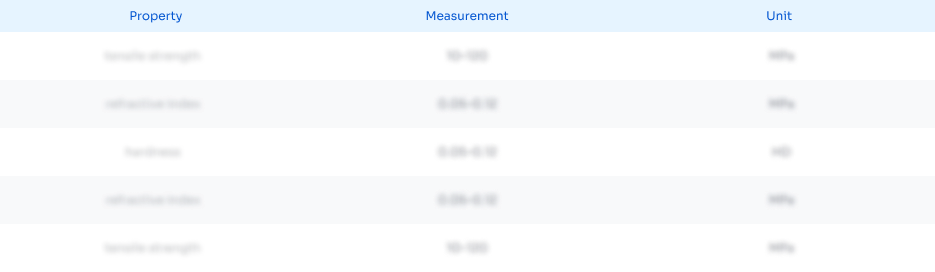
Abstract
Description
Claims
Application Information

- R&D
- Intellectual Property
- Life Sciences
- Materials
- Tech Scout
- Unparalleled Data Quality
- Higher Quality Content
- 60% Fewer Hallucinations
Browse by: Latest US Patents, China's latest patents, Technical Efficacy Thesaurus, Application Domain, Technology Topic, Popular Technical Reports.
© 2025 PatSnap. All rights reserved.Legal|Privacy policy|Modern Slavery Act Transparency Statement|Sitemap|About US| Contact US: help@patsnap.com