Method for preparing alumina by using fly ash
A technology of fly ash and alumina, applied in the preparation of alumina/aluminum hydroxide, alumina/hydroxide, etc., can solve the problems of secondary pollution, hidden safety hazards for operators, and high cost, and achieves the benefits of industrialization, Easy equipment, energy saving effect
- Summary
- Abstract
- Description
- Claims
- Application Information
AI Technical Summary
Problems solved by technology
Method used
Image
Examples
Embodiment 1
[0022] The composition of raw fly ash is: Al 2 o 3 : 41%, SiO 2 : 48%, Fe 2 o 3 : 3.3%, CaO: 3.3%, TiO 2 : 1.3%, MgO: 0.2%. The composition of the raw coal fly ash can also adopt other components and specific dosages, any conventional fly ash can be used, which cannot be used to limit the protection scope of the present invention.
[0023] Mechanically activate the fly ash, grind it to 200 mesh with a vibrating mill, mix it with water at a ratio of 1:1 and place it in an acid-resistant high-pressure reactor, and place concentrated sulfuric acid with a weight ratio of 1.5 in another pressure-resistant container connected to the reactor Inside, after the high-pressure system is closed, concentrated sulfuric acid flows into the reaction kettle where fly ash and water are mixed. The reaction kettle is lined with acid-resistant ceramic tiles, heated to 180°C, the pressure is 0.29MPa, the reaction time is 2h, and the solid-liquid separation after the reaction cools down , to o...
Embodiment 2
[0026] The raw material fly ash in Example 1 is mechanically activated, ground to 300 mesh in a vertical mill, mixed with water at a ratio of 1:1.5 and placed in an acid-resistant high-pressure reactor, and concentrated sulfuric acid with a weight ratio of 2 is placed in the reaction with In another pressure vessel connected to the kettle, after the high-pressure system is closed, the concentrated sulfuric acid flows into the reaction kettle mixed with fly ash and water. 1.5h, solid-liquid separation after the reaction cools down to obtain aluminum sulfate liquid, the solid-liquid separation equipment of aluminum sulfate solution and slag adopts pressure filtration, evaporates and concentrates, then cools, and precipitates aluminum sulfate crystals, and the liquid aluminum sulfate is evaporated and concentrated by vacuum evaporation, The lining of the evaporation equipment is made of organic materials, and a part of the leached slag is washed to neutrality, and the Al 2 o 3 a...
Embodiment 3
[0029] Mechanically activate the fly ash as the raw material in Example 1, grind it to 150 mesh in a planetary mill, mix it with water at a ratio of 1:0.5 and place it in an acid-resistant high-pressure reactor, and place concentrated sulfuric acid with a weight ratio of 1 in the reactor In another pressure-resistant container connected, after the high-pressure system is closed, the concentrated sulfuric acid flows into the reaction kettle where the fly ash and water are mixed. . After the reaction cools down, the solid-liquid is separated to obtain aluminum sulfate liquid. The solid-liquid separation equipment for aluminum sulfate solution and slag is filtered under reduced pressure. After evaporation and concentration, it is cooled to precipitate aluminum sulfate crystals. The evaporation and concentration of liquid aluminum sulfate adopts atmospheric pressure evaporation. The evaporation equipment is lined for organic materials. Take a part of the leached slag and wash it ...
PUM
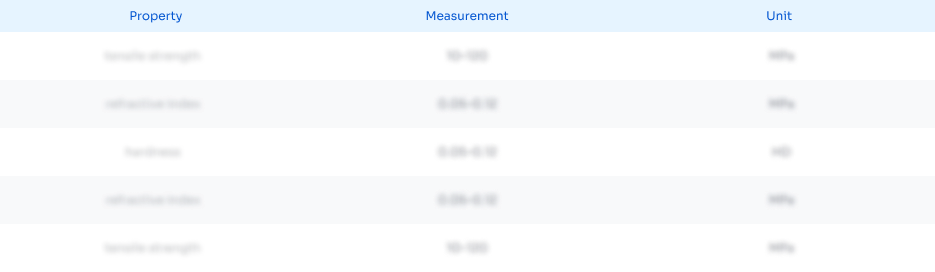
Abstract
Description
Claims
Application Information

- R&D
- Intellectual Property
- Life Sciences
- Materials
- Tech Scout
- Unparalleled Data Quality
- Higher Quality Content
- 60% Fewer Hallucinations
Browse by: Latest US Patents, China's latest patents, Technical Efficacy Thesaurus, Application Domain, Technology Topic, Popular Technical Reports.
© 2025 PatSnap. All rights reserved.Legal|Privacy policy|Modern Slavery Act Transparency Statement|Sitemap|About US| Contact US: help@patsnap.com