Brazing procedure integration device
A brazing process and brazing furnace technology, applied in the field of brazing process integrated devices, can solve the problems of incomplete cooling of workpieces, reduced workpiece quality, waste of energy, etc., and achieves reduction of labor intensity, high degree of automation, and plant saving. effect of space
- Summary
- Abstract
- Description
- Claims
- Application Information
AI Technical Summary
Problems solved by technology
Method used
Image
Examples
Embodiment Construction
[0017] like figure 1 , figure 2 The shown structure schematic diagram of the present invention comprises a brazing furnace 1, a protective atmosphere system and a heating system are arranged in the brazing furnace 1, a quenching furnace 2 is provided at one end of the discharge port of the brazing furnace 1, and a quenching furnace 2 is arranged on the top of the quenching furnace 2 A circulating fan 21, a ventilation duct 22 is laid on the bottom of the quenching furnace 2, a nozzle 221 is arranged on the ventilation duct 22, and cooling water pipes 23 are arranged on both sides of the quenching furnace 2 to ensure a stable protective atmosphere in the entire quenching furnace and low temperature state, one end of the discharge port of the quenching furnace 2 is connected to the conveying platform 5, and the conveying platform 5 is provided with a push rod mechanism. Furnace 2 housing and connected push head 41.
[0018] A gate mechanism is provided between the feed port ...
PUM
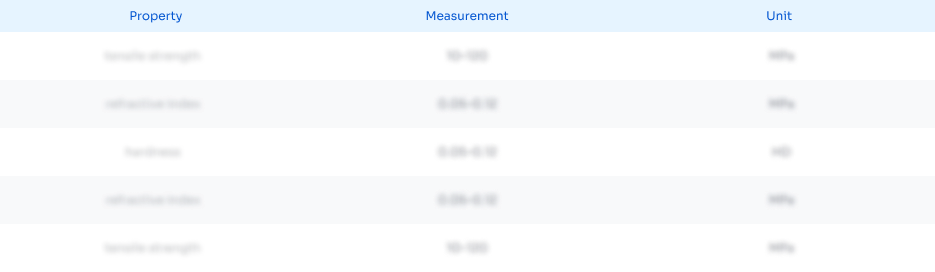
Abstract
Description
Claims
Application Information

- R&D Engineer
- R&D Manager
- IP Professional
- Industry Leading Data Capabilities
- Powerful AI technology
- Patent DNA Extraction
Browse by: Latest US Patents, China's latest patents, Technical Efficacy Thesaurus, Application Domain, Technology Topic, Popular Technical Reports.
© 2024 PatSnap. All rights reserved.Legal|Privacy policy|Modern Slavery Act Transparency Statement|Sitemap|About US| Contact US: help@patsnap.com