Preparation of blue powder for color display tube
A color display and practical technology, which is applied in the direction of chemical instruments and methods, luminescent materials, etc., can solve the problems of inability to manufacture products, and achieve the effects of improved display effect, improved coating performance, and pure color
- Summary
- Abstract
- Description
- Claims
- Application Information
AI Technical Summary
Problems solved by technology
Method used
Examples
Embodiment 1
[0026] 1) Add 0.8% zinc chloride, 1.2% potassium chloride and 1.8% sulfur to zinc sulfide, and mix them to prepare raw meal;
[0027] 2) Put the raw material into a quartz crucible and burn it at a burning temperature of 880°C and a holding time of 1.5 hours to form a powder;
[0028] 3) After removing the oxidation layer and the abnormal light-emitting part on the upper part of the powder block, continuously add deionized water, pass through a 200-mesh nylon sieve in a slurry state, and after sieving, lead into the washing tank;
[0029] 4) Add deionized water to make the slurry and deionized water reach a weight ratio of 1:6, stir for 0.2 hours; let the slurry settle completely, drain the upper clear liquid, and retain the lower slurry; repeat the above steps, , Until the conductivity of the supernatant reaches 700μS / cm;
[0030] 5) After dewatering the slurry, obtain the powder block, put the powder block into the ball mill for ball milling; add glass balls and deionized water ...
Embodiment 2
[0042] 1) Add 1.2% by weight of zinc chloride, 0.8% of potassium chloride and 2% of sulfur to zinc sulfide, and mix them evenly to prepare raw meal;
[0043] 2) Put the raw material into a quartz crucible and burn it at a burning temperature of 880°C and a holding time of 1 hour to form a powder;
[0044] 3) After removing the oxide layer and the abnormal light-emitting part on the upper part of the powder block, continuously add deionized water, pass a 100-mesh nylon sieve in a slurry state, and then introduce it into the washing tank;
[0045] 4) Add deionized water to make the slurry and deionized water reach a weight ratio of 1:6, and the stirring time is 1 hour; let stand until the slurry settles completely, drain the upper clear liquid, and retain the lower slurry; repeat the above Step, until the conductivity of the supernatant reaches 100μS / cm;
[0046] 5) Drain the supernatant liquid, get the powder after dehydration, put the powder in the ball mill and ball mill; add gla...
Embodiment 3
[0058] 1) Add 1% zinc chloride, 1% potassium chloride and 1.9% sulfur to zinc sulfide, and mix them evenly to prepare raw meal;
[0059] 2) Put the raw material into a quartz crucible and burn it at a burning temperature of 880°C and a holding time of 1.2 hours to form a powder;
[0060] 3) After removing the oxidation layer and the abnormal light-emitting part on the upper part of the powder block, continuously add deionized water, pass through a 150-mesh nylon sieve in a slurry state, and after sieving, lead into a washing tank;
[0061] 4) Add deionized water to make the slurry and deionized water reach a weight ratio of 1:6, stir, and the stirring time is 0.5 hours; let the slurry settle completely, drain the upper clear liquid, and retain the lower slurry ; Repeat the above steps until the conductivity of the supernatant is 400μS / cm;
[0062] 5) After dehydrating the slurry, obtain the powder block, put the powder block into the ball mill for ball milling; add glass balls and...
PUM
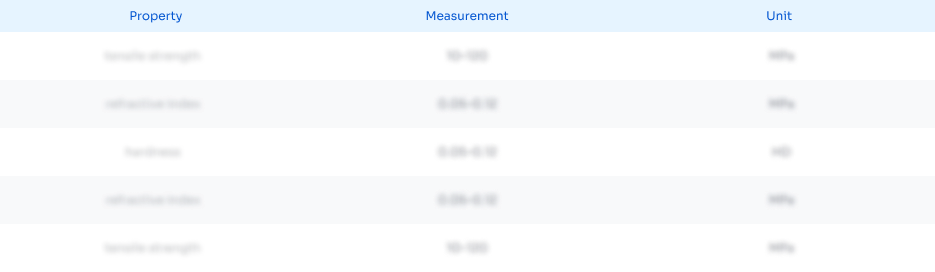
Abstract
Description
Claims
Application Information

- R&D Engineer
- R&D Manager
- IP Professional
- Industry Leading Data Capabilities
- Powerful AI technology
- Patent DNA Extraction
Browse by: Latest US Patents, China's latest patents, Technical Efficacy Thesaurus, Application Domain, Technology Topic, Popular Technical Reports.
© 2024 PatSnap. All rights reserved.Legal|Privacy policy|Modern Slavery Act Transparency Statement|Sitemap|About US| Contact US: help@patsnap.com