Method for preparing master batch with high-powder content
A content and masterbatch technology, which is applied in the field of preparing high powder content masterbatches, can solve the problems of serious material return, easy breakage of extruded material strips, and difficulty in pulling strips, so as to meet the requirements of mass production and reduce the phenomenon of material return , The effect of processing optimization
- Summary
- Abstract
- Description
- Claims
- Application Information
AI Technical Summary
Problems solved by technology
Method used
Image
Examples
Embodiment 1
[0019] Step 1, the percentage by weight of each component required for the preparation of the masterbatch
[0020] Polypropylene content 38%,
[0021] Talc content 60%,
[0022] erucamide content 1%,
[0023] Calcium stearate content 1%,
[0024] White mineral oil content 0%,
[0025] The coupling agent content is 0%.
[0026] Step 2, keep the internal mixer at a constant temperature of 180°C, add the 40% talcum powder and other components, banbury for 10 minutes, and the rotating speed of the internal mixer is 60 rpm, then add the remaining 20% talcum powder, Practice for 10 minutes.
[0027] Step 3. Turn over the compactor and turn over the hopper, pour the mixed paste into the transfer bin, use mechanical transmission to transfer the paste and pour it into the feeder through the feeding hopper, and force it through the twin-screw in the feeder The paste is pressed into the extruder, the temperature of each zone of the single-screw extruder is set at 180-200°C, and t...
Embodiment 2
[0030] Using exactly the same method and steps as in Example 1, a masterbatch with high powder content was prepared, and the masterbatch can be used for the preparation of modified polyolefin. The working parameters of each step are:
[0031] Step 1, the percentage by weight of each component required for the preparation of the masterbatch
[0032] Polyvinyl acetate content 4%,
[0033] Polyethylene content 4%,
[0034] Calcium carbonate content 90%,
[0035] Ethylene bisstearamide 1%,
[0036] White mineral oil content 1%,
[0037] The coupling agent content is 0%.
[0038] Step 2. Keep the internal mixer at a constant temperature of 100°C, add the 60% talcum powder and other components, and banbury for 10 minutes. The speed of the internal mixer is 60 rpm, then add the remaining talcum powder, and banbury for 5 minutes. minute.
[0039] Step 3. The temperature of each zone of the single-screw extruder is set to 110-130° C., and the screw speed is 80-120 rpm.
Embodiment 3
[0041] Using exactly the same method and steps as in Example 1, a masterbatch with high powder content was prepared, and the masterbatch can be used for the preparation of modified polyolefin. The working parameters of each step are:
[0042] Step 1, the percentage by weight of each component required for the preparation of the masterbatch
[0043] Polyvinyl acetate content 3%,
[0044] Polyethylene content 13%,
[0045] 80% wood flour content,
[0046] Ethylene bis stearamide content 2%,
[0047] White mineral oil content 1%,
[0048] Silane content 1%.
[0049] Step 2. Keep the internal mixer at a constant temperature of 90°C, add the 50% wood powder and other components, and banbury for 5 minutes. The speed of the internal mixer is 60 rpm, then add the remaining wood flour, and banbury for 5 minutes. .
[0050] Step 3. The temperature of each zone of the single-screw extruder is set to 120-130° C., and the screw speed is 80-120 rpm.
PUM
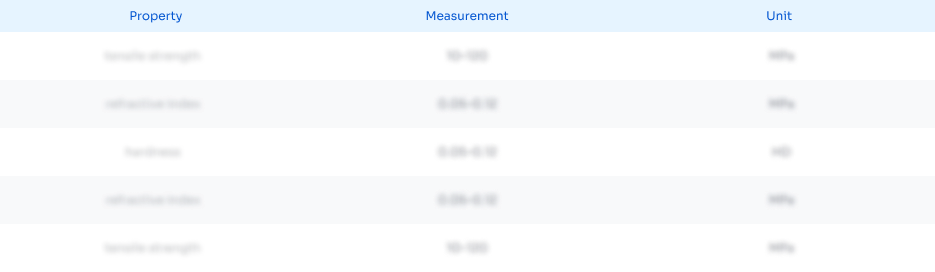
Abstract
Description
Claims
Application Information

- R&D
- Intellectual Property
- Life Sciences
- Materials
- Tech Scout
- Unparalleled Data Quality
- Higher Quality Content
- 60% Fewer Hallucinations
Browse by: Latest US Patents, China's latest patents, Technical Efficacy Thesaurus, Application Domain, Technology Topic, Popular Technical Reports.
© 2025 PatSnap. All rights reserved.Legal|Privacy policy|Modern Slavery Act Transparency Statement|Sitemap|About US| Contact US: help@patsnap.com