Acrylonitrile device tail-gas treatment technique
A technology for exhaust gas treatment and acrylonitrile, applied in the chemical industry, climate sustainability, air quality improvement and other directions, can solve the problems of high operating cost, environmental pollution, large fuel consumption, etc., achieve complete exhaust gas treatment, wide operating range, Long service life effect
- Summary
- Abstract
- Description
- Claims
- Application Information
AI Technical Summary
Problems solved by technology
Method used
Image
Examples
Embodiment 1
[0046] After the tail gas is mixed with air, it is heated by the tail gas heat exchanger 3 and / or the electric heater 4, and the inlet temperature is 280°C, and enters the catalytic oxidation reactor 5 on the precious metal platinum and palladium honeycomb metal catalyst placed in a fixed bed of catalyst. Catalytic oxidation reaction keeps the internal pressure of catalytic oxidation reactor 5 at about 16kPa (G), converts harmful volatile organic compounds into carbon dioxide and water, and releases a large amount of heat, with an outlet temperature of 650°C. The gas coming out of the catalytic oxidation reactor 5 enters the tail gas heat exchanger 3 to recover part of the heat, and the temperature is 350°C, then enters the catalytic reduction reactor 8, and performs catalytic reduction on the vanadium / titanium / tungsten ceramic honeycomb catalyst placed in the fixed bed of the catalyst reaction, keeping the pressure in the catalytic reduction reactor 8 at about 12kPa (G), the n...
Embodiment 2
[0052] Catalytic oxidation reactor 5 uses platinum honeycomb metal catalyst, the internal pressure of catalytic oxidation reactor 5 is about 5kPa(G), the inlet temperature is about 150°C, and the outlet temperature is about 460°C; catalytic reduction reactor 8 uses vanadium / titanium / tungsten For the ceramic honeycomb catalyst, the internal pressure of the catalytic reduction reactor 8 is about 3kPa (G), the inlet temperature is about 150°C, and the outlet temperature is about 160°C, and the rest are the same as in Example 1. After testing, the concentration of acrylonitrile in the purified exhaust gas is 20mg / m 3 , the nitrogen oxide content is 220mg / m 3 , the content of non-methane total hydrocarbons is 116mg / m 3 , to meet the national air pollutant comprehensive emission standards.
Embodiment 3
[0054] The catalytic oxidation reactor 5 uses palladium honeycomb metal catalyst, the internal pressure of the catalytic oxidation reactor 5 is about 10kPa(G), the inlet temperature is about 200°C, and the outlet temperature is about 510°C; the catalytic reduction reactor 8 uses vanadium / titanium / tungsten For the ceramic honeycomb catalyst, the internal pressure of the catalytic reduction reactor 8 is about 8kPa (G), the inlet temperature is about 185°C, and the outlet temperature is about 200°C, and the rest are the same as in Example 1. After testing, the concentration of acrylonitrile in the purified exhaust gas is 19mg / m 3 , the nitrogen oxide content is 200mg / m 3 , the content of non-methane total hydrocarbons is 112mg / m 3 , to meet the national air pollutant comprehensive emission standards.
PUM
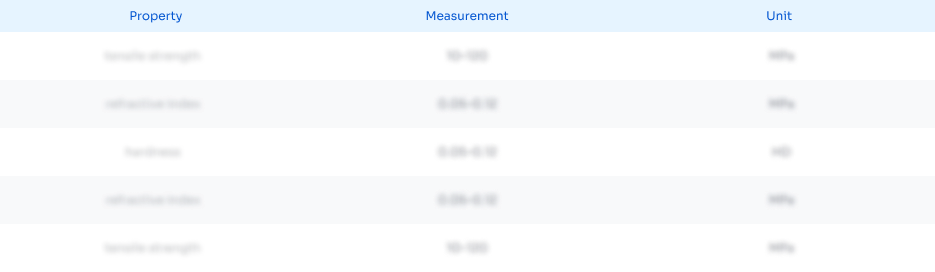
Abstract
Description
Claims
Application Information

- R&D
- Intellectual Property
- Life Sciences
- Materials
- Tech Scout
- Unparalleled Data Quality
- Higher Quality Content
- 60% Fewer Hallucinations
Browse by: Latest US Patents, China's latest patents, Technical Efficacy Thesaurus, Application Domain, Technology Topic, Popular Technical Reports.
© 2025 PatSnap. All rights reserved.Legal|Privacy policy|Modern Slavery Act Transparency Statement|Sitemap|About US| Contact US: help@patsnap.com