Moulding olivine nickel-loaded catalyst and preparation method thereof
A catalyst and olivine technology, applied in the field of biomass and coal gasification, can solve the problems of small surface area, high catalytic reaction temperature, fast catalyst deactivation, etc., achieve strong anti-carbon deposition ability, improve utilization rate, and high carbon conversion rate Effect
- Summary
- Abstract
- Description
- Claims
- Application Information
AI Technical Summary
Problems solved by technology
Method used
Examples
Embodiment 1
[0025] (1) Pulverize raw ore olivine particles into a powder of less than 300 meshes, take 7g of olivine powder, fully mix with 3g of high alumina cement, and 0.1g of charcoal powder, add 1.2g of deionized water and fully stir to form;
[0026] (2) The molded carrier was cured for 15 days, and then sintered at a high temperature of 1200° C. for 3 hours in an air atmosphere. The resulting shaped carrier is marked as S A ;
[0027] (3) impregnate the above-mentioned molding carrier with nickel nitrate aqueous solution for 2 hours, evaporate the water with a vacuum rotary evaporator, dry at 105° C. for 12 hours, and then bake at 800° C. for 4 hours in an air atmosphere;
[0028] The concentration of nickel nitrate aqueous solution is 1M;
[0029] The consumption of the nickel nitrate aqueous solution is based on the consumption of nickel oxide, which is 5 wt% of the calcined olivine-supported nickel catalyst.
[0030] The obtained catalyst is designated as A.
Embodiment 2
[0032] (1) Pulverize raw ore olivine particles into a powder of less than 300 meshes, take 8g of olivine powder, fully mix with 2g of high alumina cement, and 0.3g of charcoal powder, add 1.2g of deionized water and fully stir to form;
[0033] (2) The molded carrier was cured for 15 days, and then sintered at a high temperature of 1200° C. for 3 hours in an air atmosphere. The resulting shaped carrier is marked as S B ;
[0034] (3) Co-impregnate the above-mentioned shaped carrier with nickel nitrate and lanthanum nitrate aqueous solution for 2 hours, evaporate the water with a vacuum rotary evaporator, dry at 105°C for 12 hours, and then bake at 800°C for 4 hours in an air atmosphere;
[0035] The concentration of nickel nitrate aqueous solution is 1M;
[0036] The consumption of nickel nitrate is based on the consumption of nickel oxide, which is 8wt% after the roasting of said shaped olivine-supported nickel catalyst, and the consumption of lanthanum nitrate is based on ...
Embodiment 3
[0039] (1) Pulverize raw ore olivine particles into a powder of less than 300 meshes, take 7.5g of olivine powder, fully mix with 2g of high-alumina cement, 0.3g of carbon powder, and 0.5g of magnesium oxide, add 1.3g of deionized water and fully stir to form;
[0040] (2) The molded carrier was cured for 15 days, and then sintered at a high temperature of 1200° C. for 3 hours in an air atmosphere. The resulting shaped carrier is marked as S C ;
[0041] (3) impregnate the above-mentioned molding carrier with nickel nitrate aqueous solution for 2 hours, evaporate the water with a vacuum rotary evaporator, dry at 105° C. for 12 hours, and then bake at 800° C. for 4 hours in an air atmosphere;
[0042] The concentration of nickel nitrate aqueous solution is 1M;
[0043]The consumption of nickel nitrate is based on the consumption of nickel oxide, which is 8wt% of the said shaped olivine-supported nickel catalyst after roasting.
[0044] The obtained catalyst is designated as ...
PUM
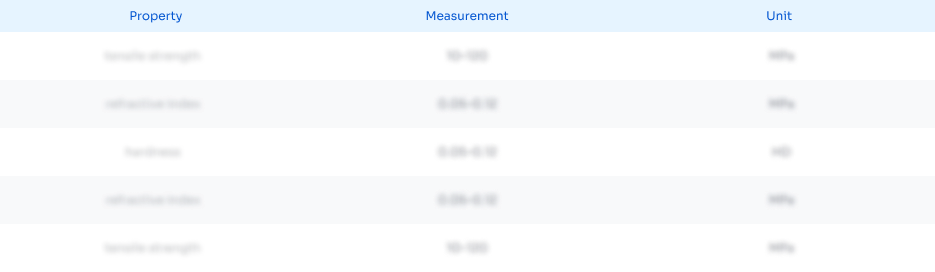
Abstract
Description
Claims
Application Information

- R&D Engineer
- R&D Manager
- IP Professional
- Industry Leading Data Capabilities
- Powerful AI technology
- Patent DNA Extraction
Browse by: Latest US Patents, China's latest patents, Technical Efficacy Thesaurus, Application Domain, Technology Topic, Popular Technical Reports.
© 2024 PatSnap. All rights reserved.Legal|Privacy policy|Modern Slavery Act Transparency Statement|Sitemap|About US| Contact US: help@patsnap.com