Catalytic composite used for ethylene rhodanate resin curing and preparation thereof
A technology of composite catalyst and cyanate ester, which is applied in the field of polymer materials, can solve problems such as the reduction of dielectric properties of resins, and achieve the effects of moderate price, high reactivity and selectivity, and good manufacturability
- Summary
- Abstract
- Description
- Claims
- Application Information
AI Technical Summary
Problems solved by technology
Method used
Image
Examples
Embodiment 1
[0019] Weigh 6.316g of dibutyltin dilaurate and 5.560g of bisphenol A type cyanate, and heat to 60°C under stirring conditions. During this process, a large amount of gas is released. When no more gas is released, the reaction is stopped to obtain Brownish yellow liquid, after cooling to room temperature, organotin compounds can be obtained.
[0020] Weigh 4.080g of cyclopentadiene manganese tricarbonyl and 5.560g of bisphenol A cyanate, dissolve them in methylene chloride at room temperature, and irradiate them under ultraviolet light for 10 minutes to obtain a tan liquid, namely cyclopentadiene Diene manganese tricarbonyl complex solution.
[0021] The organotin compound and cyclopentadiene manganese tricarbonyl complex were mixed at a molar ratio of tin to manganese of 1:10, dissolved in dichloromethane, and stirred for 5 minutes to obtain a composite catalyst.
[0022] Weigh 55.6g (0.2mol) of bisphenol A type cyanate and place it in a beaker, heat it to 90°C and melt it, ...
Embodiment 2
[0025] According to the method of Example 1, an organotin compound and a cyclopentadiene manganese tricarbonyl complex were prepared.
[0026] The organotin compound and cyclopentadiene manganese tricarbonyl complex were mixed at a molar ratio of tin to manganese of 1:15, dissolved in acetone, and stirred for 7 minutes to obtain a composite catalyst.
Embodiment 3
[0028] According to the method of Example 1, an organotin compound and a cyclopentadiene manganese tricarbonyl complex were prepared.
[0029] The organotin compound and cyclopentadiene manganese tricarbonyl complex were mixed at a molar ratio of tin to manganese of 1:20, dissolved in dichloromethane, and stirred for 10 minutes to obtain a composite catalyst.
[0030] Weigh 55.6g (0.2mol) of bisphenol A type cyanate and place it in a beaker, heat it to 90°C and melt it, add 0.002mol of the above-mentioned composite catalyst (calculated by the number of moles of Mn), and stir evenly to obtain uncured Catalyzed resin, its gel time curve see figure 1 Curve c in.
[0031] Pour the uncured catalytic resin into the pre-treated mold, vacuum defoam for 30min, then cure according to the process of 150℃ / 1h+180℃ / 2h, and post-treat at 200℃ for 2h to obtain the cyanide catalyzed by the composite catalyst Ester cured resin, its dielectric properties see figure 2 .
PUM
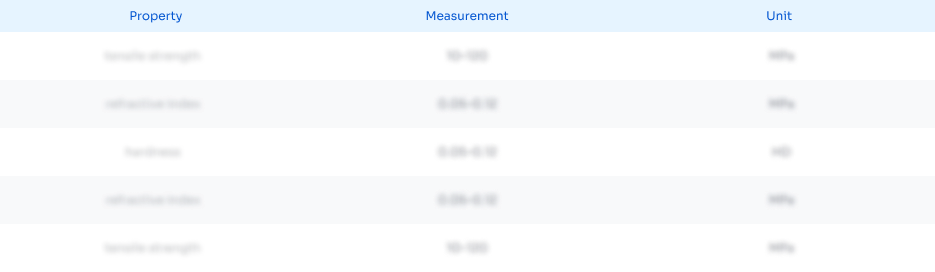
Abstract
Description
Claims
Application Information

- R&D Engineer
- R&D Manager
- IP Professional
- Industry Leading Data Capabilities
- Powerful AI technology
- Patent DNA Extraction
Browse by: Latest US Patents, China's latest patents, Technical Efficacy Thesaurus, Application Domain, Technology Topic, Popular Technical Reports.
© 2024 PatSnap. All rights reserved.Legal|Privacy policy|Modern Slavery Act Transparency Statement|Sitemap|About US| Contact US: help@patsnap.com