Method for manufacturing linear change gradient coating of TiAlCN non-metallic element
A non-metal element and gradient coating technology, which is applied in metal material coating process, coating, ion implantation plating, etc., can solve the problem of insufficient stability of film performance, large internal stress of multi-layer coating, and easy oxidation of the film layer etc. to achieve excellent surface finish, reduce residual stress, and improve tool cutting performance
- Summary
- Abstract
- Description
- Claims
- Application Information
AI Technical Summary
Problems solved by technology
Method used
Examples
Embodiment 1
[0044] Embodiment 1, a method for making a TiAlCN non-metallic element linear change gradient coating of the present invention is to use the PVD method for coating treatment. The coating treatment process is divided into four consecutive time periods, and the process includes the following steps :
[0045] a. In the first period of time, only nitrogen N2 is passed into the furnace cavity, the flow rate of nitrogen N2 is 500sccm, the evaporation current of Ti target is 170A, and the temperature is 350℃~450℃, so that the surface of the substrate is coated with a Layer height and dense TiN intermediate layer, the thickness of the TiN intermediate layer is 0.2~0.8um;
[0046] b. In the second period of time, argon Ar, nitrogen N2, and acetylene gas C2H2 are introduced into the furnace cavity at the same time, the flow rate of argon Ar is controlled at 700 sccm and remains unchanged, the evaporation current of the TiAl alloy target is 140A, and the temperature is controlled At 430...
Embodiment 2
[0058] Embodiment 2, a method for making a TiAlCN non-metallic element linear change gradient coating of the present invention, differs from Embodiment 1 in that:
[0059] In step a, the flow rate of nitrogen N2 is 400 sccm, and the evaporation current of Ti target is 160A;
[0060] In step b, the flow rate of argon gas Ar remains constant at 800 sccm, and the evaporation current of the TiAl alloy target is 130 A; as the coating progresses, the flow rate of nitrogen N2 drops from 480 sccm to 140 sccm at a constant speed, and the flow rate of acetylene gas C2H2 decreases from 8 sccm Rise to 75sccm at a constant speed;
[0061] In step c, the flow rate of argon gas Ar is adjusted from 800 sccm to 600 sccm at a constant speed, the flow rate of nitrogen N2 is adjusted from 140 sccm to 350 sccm at a constant speed, the flow rate of acetylene gas C2H2 is adjusted from 75 sccm to 150 sccm at a constant speed, and the evaporation current of the TiAl alloy target is 130A;
[0062] In ...
Embodiment 3
[0064] Embodiment three, a kind of TiAlCN nonmetallic element linear change gradient coating manufacturing method of the present invention, differs from embodiment one in that:
[0065] In step a, the flow rate of nitrogen N2 is 550 sccm, and the evaporation current of Ti target is 180A;
[0066] In step b, the flow of argon Ar is kept constant at 500 sccm, and the evaporation current of the TiAl alloy target is 150 A; as the coating progresses, the flow of nitrogen N2 drops from 520 sccm to 160 sccm at a constant speed, and the flow of acetylene gas C2H2 decreases from 12 sccm Rise to 85sccm at a constant speed;
[0067] In step c, the flow rate of argon gas Ar is adjusted from 500 sccm to 600 sccm at a constant speed, the flow rate of nitrogen N2 is adjusted from 160 sccm to 350 sccm at a constant speed, the flow rate of acetylene gas C2H2 is adjusted from 85 sccm to 150 sccm at a constant speed, and the evaporation current of the TiAl alloy target is 150A;
[0068] In the ...
PUM
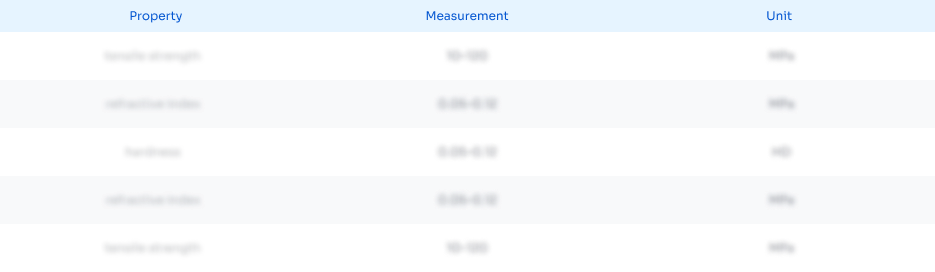
Abstract
Description
Claims
Application Information

- R&D Engineer
- R&D Manager
- IP Professional
- Industry Leading Data Capabilities
- Powerful AI technology
- Patent DNA Extraction
Browse by: Latest US Patents, China's latest patents, Technical Efficacy Thesaurus, Application Domain, Technology Topic, Popular Technical Reports.
© 2024 PatSnap. All rights reserved.Legal|Privacy policy|Modern Slavery Act Transparency Statement|Sitemap|About US| Contact US: help@patsnap.com