Zinc-aluminum-copper-titanium-neodymium spray coating alloy solder and method of manufacturing the same
A copper-titanium, zinc-aluminum technology, applied in welding equipment, metal processing equipment, welding/cutting media/materials, etc., to achieve the effects of high mechanical strength, improved service life, and strong adhesion
- Summary
- Abstract
- Description
- Claims
- Application Information
AI Technical Summary
Problems solved by technology
Method used
Image
Examples
Embodiment 1
[0021] Raw materials (kg): aluminum 4.0, copper 0.5, titanium 1.5, neodymium 0.05, zinc 94.04.
[0022] Preparation method: Heat and melt the zinc block and continue to raise the temperature and keep it at 680±20°C. Bind the titanium block to the lower end of the stainless steel stirring rod with a 1kg copper wire, press it into the molten zinc solution and corrode for 1 hour, then stir for 0.5 hour. Use copper foil to wrap the neodymium rare earth metals taken out of kerosene quickly and tightly, then wrap tightly with 2kg aluminum foil on the outer layer, use 1kgφ2mm copper wire to bind the wrapped neodymium package to the lower end of the stainless steel stirring rod, and press it into the above In the molten zinc solution, after 1 hour of erosion, stir for 1 hour to obtain the zinc-aluminum-copper-titanium-neodymium-neodymium gold-sprayed solder. The erosion and stirring time should be sufficient to ensure the completion of the reaction and the uniformity and stability of ...
Embodiment 2
[0024] Raw materials (kg): aluminum 4.5, copper 0.8, titanium 0.06, neodymium 0.1, zinc 94.04.
[0025] Preparation method: heat and melt the zinc block and continue to heat up and keep it at 600°C; bind the titanium block to the lower end of the stainless steel stirring rod with 2kg copper wire, press it into the molten zinc solution for corrosion for 2 hours, and stir for 1 hour. Use copper foil to wrap the neodymium rare earth metals taken out of kerosene quickly and tightly, then wrap tightly with 1kg aluminum foil on the outer layer, use 1kgφ2mm copper wire to bind the wrapped neodymium package to the lower end of the stainless steel stirring rod, and press it into the above In the molten zinc solution, after melting for 2 hours, stir for 1.5 hours to obtain zinc-aluminum-copper-titanium-neodymium-sprayed gold solder.
Embodiment 3
[0027] Raw materials (kg): aluminum 5.0, copper 1.0, titanium 0.09, neodymium 0.05, zinc 93.06.
[0028] Preparation method: with embodiment 1.
PUM
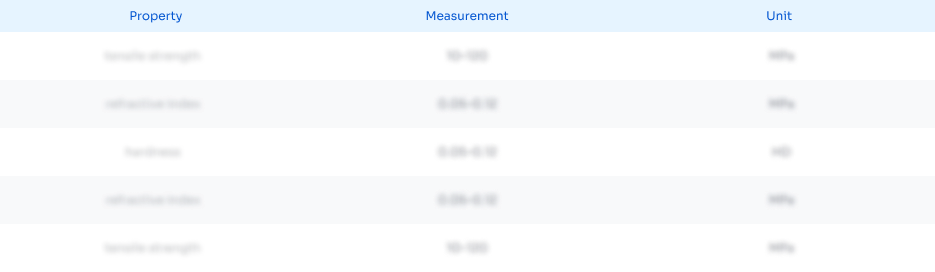
Abstract
Description
Claims
Application Information

- Generate Ideas
- Intellectual Property
- Life Sciences
- Materials
- Tech Scout
- Unparalleled Data Quality
- Higher Quality Content
- 60% Fewer Hallucinations
Browse by: Latest US Patents, China's latest patents, Technical Efficacy Thesaurus, Application Domain, Technology Topic, Popular Technical Reports.
© 2025 PatSnap. All rights reserved.Legal|Privacy policy|Modern Slavery Act Transparency Statement|Sitemap|About US| Contact US: help@patsnap.com