Preparation method for porous titanium and porous titanium alloy
A technology of titanium alloy and porous titanium, which is applied in the field of preparation of porous titanium and porous titanium alloy, can solve the problems of lack of system, no characterization of coating performance, single spraying process and heat treatment process, etc., to achieve simple process and short production cycle , good controllability
- Summary
- Abstract
- Description
- Claims
- Application Information
AI Technical Summary
Problems solved by technology
Method used
Image
Examples
Embodiment 1
[0024] Choose 11-45μm titanium powder. The substrate is a 45mm×30mm×4mm low-carbon steel plate, and the surface is roughened with -100 mesh alumina fine sand before spraying. The working gas of cold spraying is compressed air, the gas pressure at the inlet of the spray gun is 2.7MPa, and the gas temperature is 500-520°C; the powder feeding gas is argon, the pressure is 3.0MPa; the powder feeding rate is about 30g / min; the spraying distance is 30mm, and the moving speed of the spray gun is 150mm / s. The thickness of the coating layer is about 5mm. After spraying, the substrate is peeled off, and then vacuum heat treatment is carried out, the heat treatment temperature is 850°C, the heat preservation time is 4 hours, and then cooled to room temperature with the furnace. Observe the coating section structure, such as figure 2 It can be seen that the distribution of pores in the coating is relatively uniform. The average porosity of the sprayed state is about 11%, and the ave...
Embodiment 2
[0026] Choose 45-160μm titanium powder. The substrate is a 45mm×30mm×4mm low-carbon steel plate, and the surface is roughened with -100 mesh alumina fine sand before spraying. The working gas of cold spraying is compressed air, the gas pressure at the inlet of the spray gun is 2.8MPa, and the gas temperature is about 550°C; the powder feeding gas is argon, the pressure is 3.1Mpa; the powder feeding rate is about 30g / min; the spraying distance is 30mm, and the moving speed of the spray gun is 150mm / s. The thickness of the coating layer is about 5mm. After spraying, the substrate is peeled off, and then vacuum heat treatment is carried out, the heat treatment temperature is 850°C, the heat preservation time is 4 hours, and then cooled to room temperature with the furnace. Observe the coating section structure, such as image 3 It can be seen that the distribution of pores in the coating is relatively uniform. The average porosity of the sprayed state is about 15%, and the a...
Embodiment 3
[0028] Choose 11-63μm Ti-6Al-4V powder. The substrate is a 45mm×30mm×4mm low-carbon steel plate, and the surface is roughened with -100 mesh alumina fine sand before spraying. The working gas for cold spraying is compressed air, the gas pressure at the inlet of the spray gun is 2.8MPa, and the gas temperature is about 550°C; the powder feeding gas is argon, the pressure is 3.1MPa; the powder feeding rate is about 30g / min; the spraying distance is 30mm, and the moving speed of the spray gun is 150mm / s. The thickness of the coating layer is about 5mm. After spraying, the substrate is peeled off, and then vacuum heat treatment is carried out, the heat treatment temperature is 850°C, the heat preservation time is 4 hours, and then cooled to room temperature with the furnace. Observe the coating section structure, such as Figure 4 It can be seen that the distribution of pores in the coating is relatively uniform. Because the titanium alloy has high strength and poor deformati...
PUM
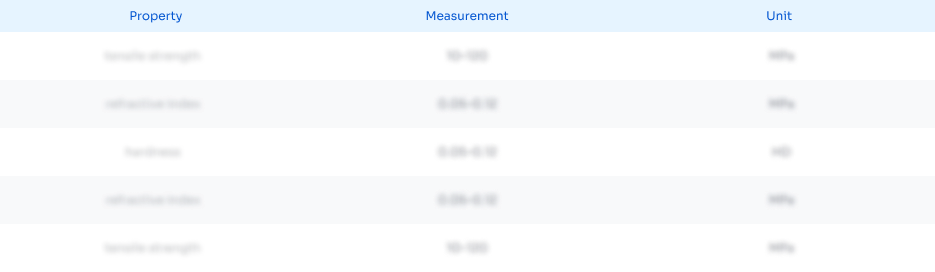
Abstract
Description
Claims
Application Information

- Generate Ideas
- Intellectual Property
- Life Sciences
- Materials
- Tech Scout
- Unparalleled Data Quality
- Higher Quality Content
- 60% Fewer Hallucinations
Browse by: Latest US Patents, China's latest patents, Technical Efficacy Thesaurus, Application Domain, Technology Topic, Popular Technical Reports.
© 2025 PatSnap. All rights reserved.Legal|Privacy policy|Modern Slavery Act Transparency Statement|Sitemap|About US| Contact US: help@patsnap.com