High electric insulation sealing method for anodized aluminum film
An anodized aluminum, high temperature sealing technology, applied in electrolytic coatings, surface reaction electrolytic coatings, coatings, etc., can solve the problem of less research and application of insulating aluminum oxide film sealing technology, high production cost, long sealing time, etc. problems, to achieve the effect of excellent sealing effect, short high temperature sealing time and short sealing time
- Summary
- Abstract
- Description
- Claims
- Application Information
AI Technical Summary
Problems solved by technology
Method used
Examples
Embodiment 1
[0027] In this embodiment, the sample material is pure aluminum (biling aluminum, aluminum content ≥ 99.7%), the sample is taken from the production line of anodic oxidation insulating film of aluminum wire, and its anodic oxidation electrolyte is a mixed acid solution, the mixed acid The formula of solution is: sulfuric acid 20% (volume ratio), oxalic acid 18g / L, nickel sulfate 8g / L, additive 0.1g / L. The process conditions are: AC oxidation, current density 2.8A / dm 2 , the oxidation time is 30min, the cathode material is lead plate or graphite plate, the breakdown voltage of the film layer is required to be ≥500V, and the mass loss per unit area Δm≤9×10-7 g / mm 2 . The size of the cut sample is 100mm×10mm×2mm, and the calculated surface area of the sample is A=2400mm 2 . The aluminum oxide film on the surface of the sample is sealed as follows:
[0028] 1) Preparation of blocking solution
[0029] First, prepare a normal-temperature sealing solution: 3 L of nickel-fluor...
Embodiment 2
[0038] In this embodiment, the sample material is industrial aluminum foil (aluminum content is 99.5%), and its anodic oxidation electrolyte is a mixed acid solution, and its formula is: sulfuric acid 20% (volume ratio), oxalic acid 18g / L, nickel sulfate 8g / L , Additive 0.1g / L. The process conditions are: AC oxidation, current density 2.8A / dm 2 , Oxidation time 30min, cathode material cliche or graphite plate. The film breakdown voltage is required to be ≥350V. Mass loss per unit area Δm≤9×10 -7 g / mm 2 . The size of the intercepted sample is 100mm×100mm, and the calculated surface area of the sample is 20000mm 2 . The aluminum oxide film on the surface of the sample is sealed as follows:
[0039] 1) Preparation of blocking solution
[0040] First prepare the normal temperature sealing solution: the sealing solution contains 6.5g of nickel acetate per liter, sodium fluoride: 1.5g, isoamyl alcohol: 4g, octylphenol polyoxyethylene ether: 0.3g, and prepare the nickel-flu...
Embodiment 3
[0049] In this embodiment, the sample material is pure aluminum (biling aluminum, aluminum content ≥ 99.7%), the sample is taken from the production line of anodic oxidation insulating film of aluminum wire, and its anodic oxidation electrolyte is a mixed acid solution, the mixed acid The formula of solution is: sulfuric acid 20% (volume ratio), oxalic acid 18g / L, nickel sulfate 8g / L, additive 0.1g / L, current density 2.8A / dm 2 . The process conditions are: alternating current oxidation, oxidation time 30min, the cathode material is lead plate or graphite plate, the breakdown voltage of the film layer is required to be ≥500V, and the mass loss per unit area Δm≤9×10 -7 g / mm 2 . The size of the intercepted sample is 100mm×160mm×2mm, and the calculated surface area of the sample is A=3600mm 2 . The aluminum oxide film on the surface of the sample is sealed as follows:
[0050] 1) Preparation of blocking solution
[0051] First prepare the normal temperature sealing solutio...
PUM
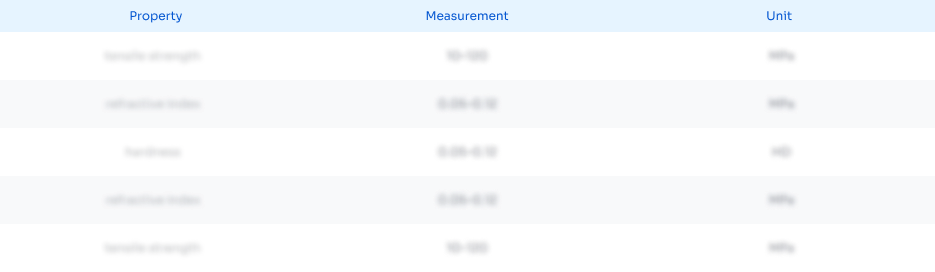
Abstract
Description
Claims
Application Information

- R&D Engineer
- R&D Manager
- IP Professional
- Industry Leading Data Capabilities
- Powerful AI technology
- Patent DNA Extraction
Browse by: Latest US Patents, China's latest patents, Technical Efficacy Thesaurus, Application Domain, Technology Topic, Popular Technical Reports.
© 2024 PatSnap. All rights reserved.Legal|Privacy policy|Modern Slavery Act Transparency Statement|Sitemap|About US| Contact US: help@patsnap.com