Manufacturing technique for oxygen-enriched side blowing molten pool raw copper smelting and special equipment thereof
A melting pool smelting and production process technology, applied in the field of copper smelting, can solve the problems of coal-fired flue gas exhaustion that aggravates environmental pollution, high energy consumption of closed blast furnaces, and heavy caking of straight-up flue, so as to facilitate large-scale production , good environmental protection effect and compact structure
- Summary
- Abstract
- Description
- Claims
- Application Information
AI Technical Summary
Problems solved by technology
Method used
Image
Examples
Embodiment 1
[0043] Embodiment 1: a kind of production technique of smelting blister copper in oxygen-enriched side-blown molten pool (see figure 1 ), including the following steps:
[0044] Copper concentrate smelting:
[0045] According to weight percentage, 75% of copper concentrate, 1% of soot, 6% of fine slag, 8% of quartz stone, 4% of limestone, and 6% of pulverized coal are mixed evenly and then fed into the side-blown furnace from the furnace top feed port through the feed belt. High-pressure (0.18Mpa) oxygen-enriched air (oxygen concentration 45%) is blown into the wind eye to form a violent agitation for the melt in the molten pool, and the mass and heat transfer processes in the molten pool are carried out rapidly, completing a series of chemical reactions and forming Copper matte (grade 65%), slag and high-temperature flue gas (1100°C-1200°C), copper matte and slag flow into the depleted electric furnace continuously through the chute, and the high-temperature flue gas recover...
Embodiment 2
[0050] Embodiment 2: a kind of production technique of smelting blister copper in oxygen-enriched side-blown molten pool (see figure 1 ), including the following steps:
[0051] Copper concentrate smelting:
[0052] According to weight percentage, 80% of copper concentrate, 2% of soot, 2% of fine slag, 4% of quartz stone, 5% of limestone, and 7% of pulverized coal are mixed evenly and fed into the side-blowing furnace through the feeding belt through the feeding port on the top of the furnace. High-pressure (0.17Mpa) oxygen-enriched air (oxygen concentration 38%) is blown into the wind eye to form a violent agitation for the melt in the molten pool, and the mass and heat transfer processes in the molten pool are carried out rapidly, completing a series of chemical reactions and forming Copper matte (grade 58%), slag and high-temperature flue gas (1100°C-1200°C), copper matte and slag flow into the depleted electric furnace continuously through the chute, and high-temperature ...
Embodiment 3
[0057] Embodiment 3: a kind of production technique of smelting blister copper in oxygen-enriched side-blown molten pool (see figure 1 ), including the following steps:
[0058] Copper concentrate smelting:
[0059] 85% of copper concentrate, 4% of quartz stone, 5% of limestone, and 6% of pulverized coal are mixed according to weight percentage. ) Oxygen-enriched air (oxygen concentration 30%) forms violent stirring to the melt in the molten pool, and the mass transfer and heat transfer processes in the molten pool proceed rapidly, completing a series of chemical reactions to form copper matte (grade 50%), slag And high-temperature flue gas (1100°C-1200°C), copper matte and slag flow into the depleted electric furnace continuously from the chute, and the high-temperature flue gas recovers waste heat and sends it to acid production.
[0060] Slag depletion:
[0061] After the copper matte and slag flow into the depleted electric furnace, the slag is clarified and separated f...
PUM
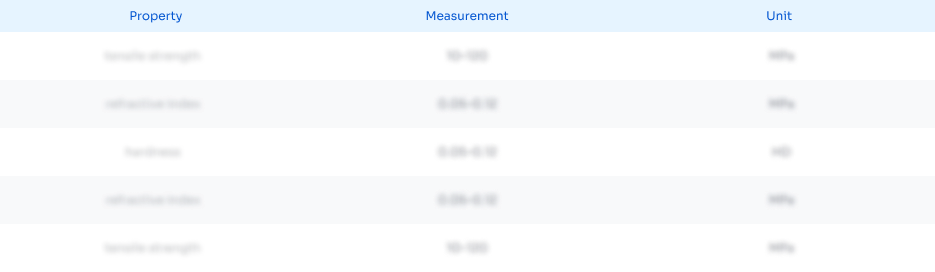
Abstract
Description
Claims
Application Information

- R&D
- Intellectual Property
- Life Sciences
- Materials
- Tech Scout
- Unparalleled Data Quality
- Higher Quality Content
- 60% Fewer Hallucinations
Browse by: Latest US Patents, China's latest patents, Technical Efficacy Thesaurus, Application Domain, Technology Topic, Popular Technical Reports.
© 2025 PatSnap. All rights reserved.Legal|Privacy policy|Modern Slavery Act Transparency Statement|Sitemap|About US| Contact US: help@patsnap.com