Hot working method for smelting molybdenum rhenium alloy casting ingot by suspending
A molybdenum-rhenium alloy and suspension smelting technology, which is applied in the field of metal pressure processing, can solve problems such as difficult pressure processing, intergranular splitting, and coarse grains of ingots, so as to reduce the amount of dislocation movement, avoid impact, and avoid cracks Effect
- Summary
- Abstract
- Description
- Claims
- Application Information
AI Technical Summary
Problems solved by technology
Method used
Examples
Embodiment 1
[0016] In terms of weight percentage, Mo59% and Re41% in molybdenum-rhenium alloy, put the sintered molybdenum-rhenium alloy bar into a vacuum furnace for electron beam suspension melting to obtain a Φ30×300mm ingot; hot rolling on a plate rolling mill, heating in a hydrogen furnace, The temperature is 1200°C to 1800°C, and the temperature is kept for 1 hour. The first fire is rolled parallel to the ingot and fed axially, the roll line speed is 400mm / min, and is rolled to a thickness of 15mm through three passes. The second heat is heated to 1200°C to 1800°C, and the temperature is maintained for 1 hour. The linear speed of the roll is 400mm / min, and the vertical ingot is fed and rolled to a thickness of 7mm. The heating temperature of the third fire is 1100 ℃ ~ 1700 ℃, heat preservation for 30 minutes, rolling to a thickness of 3mm, annealing and then cold rolling. Qualified molybdenum-rhenium alloy plates with fine grains and uniform size are obtained, with a purity of over...
Embodiment 2
[0018] In terms of weight percentage, Mo75% and Re25% in molybdenum-rhenium alloy, the molybdenum-rhenium alloy sintered strip is put into a vacuum furnace for electron beam suspension melting to obtain a Φ30×300mm ingot, which is hot-rolled on a plate rolling mill and heated by a hydrogen furnace. The temperature is 1200°C to 1800°C, and the temperature is kept for 1 hour. The first fire is rolled parallel to the ingot and fed axially, the roll line speed is 400mm / min, and the thickness is 15mm after three passes. The heating temperature of the second fire is 1200°C-1800°C, heat preservation for 1 hour, the linear speed of the roll is 400mm / min, and the vertical feeding and rolling of the axial direction of the ingot reaches a thickness of 7mm. The heating temperature of the third fire is 1100 ℃ ~ 1700 ℃, heat preservation for 30 minutes, rolling to 3mm thickness, annealing and then cold rolling, and the qualified molybdenum-rhenium alloy plate with fine grain and uniform siz...
Embodiment 3
[0020] In terms of weight percentage, Mo59% and Re41% in molybdenum-rhenium alloy, the molybdenum-rhenium alloy sintered bar is put into a vacuum furnace for electron beam suspension melting, and the ingot size is Φ45×300mm; it is hot-rolled on a plate rolling mill and heated by a hydrogen furnace , temperature 1200 ℃ ~ 1800 ℃, heat preservation for 1 hour, roll line speed 300mm / min, the first fire rolling parallel ingot axial feeding, after three passes to 25mm thick. The second fire time is 1200℃~1800℃, heat preservation for 1 hour, the linear speed of the roll is 300mm / min, and the vertical ingot is axially fed and rolled to a thickness of 10mm. The third fire time is 1100℃~1700℃, heat preservation for 30 minutes, rolling speed 400mm / min, rolling to 3mm thickness in three passes, then cold rolling after annealing, to obtain qualified molybdenum-rhenium alloy plates with fine grains and uniform size. The purity is over 99.99%.
PUM
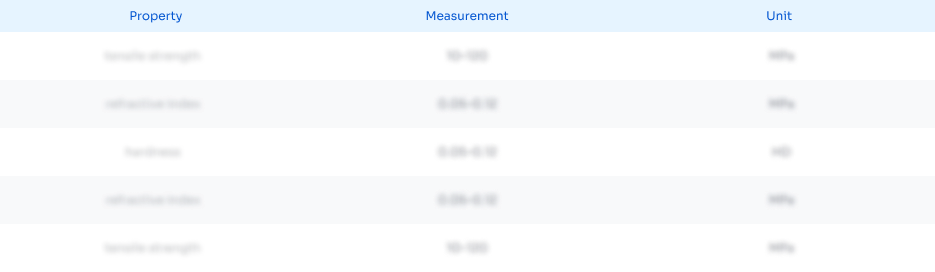
Abstract
Description
Claims
Application Information

- Generate Ideas
- Intellectual Property
- Life Sciences
- Materials
- Tech Scout
- Unparalleled Data Quality
- Higher Quality Content
- 60% Fewer Hallucinations
Browse by: Latest US Patents, China's latest patents, Technical Efficacy Thesaurus, Application Domain, Technology Topic, Popular Technical Reports.
© 2025 PatSnap. All rights reserved.Legal|Privacy policy|Modern Slavery Act Transparency Statement|Sitemap|About US| Contact US: help@patsnap.com