Ferrotitanium alloy electric induction furnace smelting method
An induction electric furnace and ferro-titanium technology, which is applied in the field of metal smelting, can solve the problems of inability to smelt rutile-type ferro-titanium alloy, difficulty in producing products, and high production costs, and achieve the effect of simple process, easy operation and low cost
- Summary
- Abstract
- Description
- Claims
- Application Information
AI Technical Summary
Problems solved by technology
Method used
Examples
Embodiment 1
[0028] The ferro-titanium alloy induction furnace smelting method includes the following process steps:
[0029] Step 1: Add ilmenite, rutile, quicklime, steel, ferrosilicon and other minerals into the crucible of an ordinary induction furnace according to the following proportions, and heat to 1800-1900°C to completely melt the minerals in the crucible;
[0030] Raw material proportioning of the present invention is:
[0031] Titanium concentrate (TiO 2 ≥46) 50~55 parts by weight
[0032] Rutile (TiO 2 ≥90%) 15~18 parts by weight
[0033] Quicklime (CaO≥87%) 5-6 parts by weight
[0034] Steel 4-5 parts by weight
[0035] Ferrosilicon (Si≥73%) 1-2 parts by weight
[0036] Aluminum particles (Al≥97%) 44-50 parts by weight
[0037] Potassium chlorate (KClO 3 ≥98%) 1.6~2 parts by weight
[0038] Step 2: Pour the completely melted ore in the crucible of an ordinary induction furnace into a high-temperature-resistant smelting furnace or crucible that can withstand temperat...
Embodiment 2
[0041] The ratio of raw materials for ferro-titanium alloy induction furnace smelting method is:
[0042] Titanium concentrate (TiO 2 ≥46) 65~70 parts by weight
[0043] Rutile (TiO 2 ≥90%) 25~30 parts by weight
[0044] Quicklime (CaO≥87%) 8-10 parts by weight
[0045] Steel 7-8 parts by weight
[0046] Ferrosilicon (Si≥73%) 5-6 parts by weight
[0047] Aluminum particles (Al≥97%) 55-60 parts by weight
[0048] Potassium chlorate (KClO 3 ≥98%) 2.6~3 parts by weight
[0049] Its processing step is identical with embodiment 1.
[0050] The present invention has been successfully applied to a 1000Kg intermediate frequency induction furnace to produce ferro-titanium alloy with a titanium content of 41%. The economic indicators are as follows:
[0051] Furnace output: 0.5 tons / furnace
[0052] Daily output: 4 tons
[0053] Unit power consumption: 2800~3000KW·h / ton
[0054] Titanium content in the alloy: 40-41%
[0055] Impurity content: lower than the national standar...
PUM
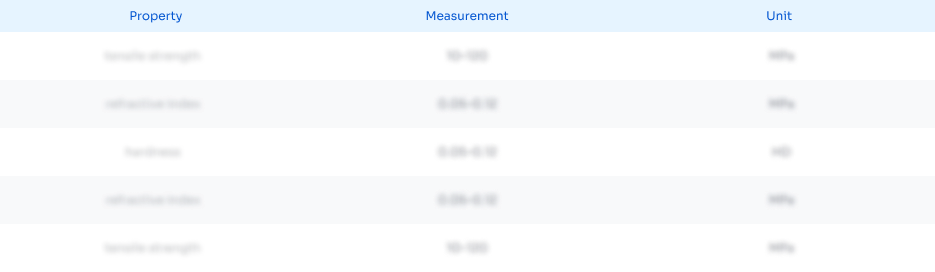
Abstract
Description
Claims
Application Information

- R&D
- Intellectual Property
- Life Sciences
- Materials
- Tech Scout
- Unparalleled Data Quality
- Higher Quality Content
- 60% Fewer Hallucinations
Browse by: Latest US Patents, China's latest patents, Technical Efficacy Thesaurus, Application Domain, Technology Topic, Popular Technical Reports.
© 2025 PatSnap. All rights reserved.Legal|Privacy policy|Modern Slavery Act Transparency Statement|Sitemap|About US| Contact US: help@patsnap.com