Method for producing biomass carbonization carbon and biomass gas, and rapid thermal decomposition coke oven
A biomass gas and biomass technology, which is applied in the fields of biofuels, special forms of dry distillation, combined combustion mitigation, etc., can solve the problems of uneven distribution of high-temperature gas, high price, and large unsafe factors, and achieves loose and porous carbon. Good surface properties, high carbon content effect
- Summary
- Abstract
- Description
- Claims
- Application Information
AI Technical Summary
Problems solved by technology
Method used
Image
Examples
Embodiment 1
[0015]Materials such as rice husks and fruit husks (moisture content is controlled at about 10%) are fed into the upper part of the furnace (Φ1.6 meters in diameter and 5.3 meters in height) through the feeding nozzle 2 in the middle of the upper part of the upper furnace roof 4. The collection chamber 5 is distributed into the dry distillation carbonization chamber 10 and the gasification reaction chamber 11. After the materials are filled, the feeding sealing valve 1 is closed, the air inlet nozzle arranged at the bottom of the gasification reaction chamber is opened, and the gasification chamber arranged outside the furnace is activated. Negative-pressure Roots blower, then open the furnace door 14 arranged at the bottom of the gasification reaction chamber; ignite the gasified material in the gasification reaction chamber, and close the furnace door 14; under the action of the negative-pressure Roots blower outside the furnace, suction The 500-700C high-temperature oxygen-d...
Embodiment 2
[0018] Cotton stalks, corn stalks, soybean stalks, and sorghum stalks are used as the main materials. After processing and cutting, the length is controlled at 30-50 mm, and the water content is controlled at about 10%. 2 Feed into the furnace (Φ diameter 2.4 meters, furnace body height 5.6 meters) in the upper collection chamber 5 in the furnace and distribute into the retort carbonization chamber 10 and gasification reaction chamber 11. After the materials are filled, close the feeding sealing valve 1 and open The air inlet nozzle arranged at the bottom of the gasification reaction chamber starts the negative pressure Roots blower arranged outside the furnace, and then opens the furnace door 14 arranged at the lower part of the gasification reaction chamber; ignites the gasified materials in the gasification reaction chamber, and closes Furnace door 14; under the action of the negative pressure Roots blower outside the furnace, the 500-700C ° high-temperature oxygen-deficient...
Embodiment 3
[0021] The main materials are rice straw, thatch, wheat straw, rapeseed stalk, and bagasse. After they are chopped or crushed, dried, they are mechanically extruded into block or rod-shaped materials. The water content is controlled at about 10%. The upper middle charging nozzle 2 arranged on the upper furnace roof 4 is fed into the furnace (3.3 meters in diameter, 5.8 meters in height of the furnace body) and the upper collection chamber 5 in the furnace is distributed into the dry distillation carbonization chamber 10 and the gasification reaction chamber 11. After the material is filled up, close the feeding sealing valve 1, open the air inlet nozzle arranged at the bottom of the gasification reaction chamber, start the negative pressure Roots blower arranged outside the furnace, and then open the furnace door 14 arranged at the lower part of the gasification reaction chamber ignite the gasified material in the lower part of the gasification reaction chamber, and close the f...
PUM
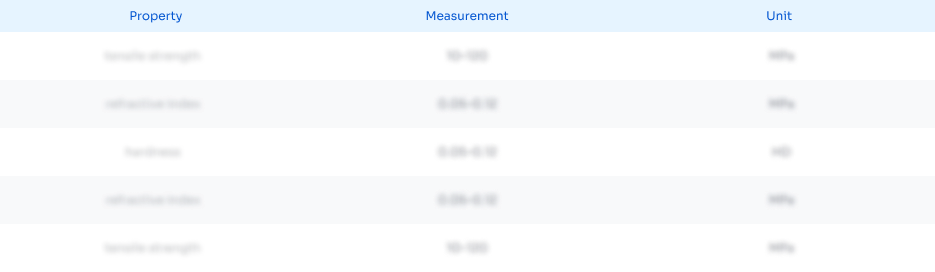
Abstract
Description
Claims
Application Information

- Generate Ideas
- Intellectual Property
- Life Sciences
- Materials
- Tech Scout
- Unparalleled Data Quality
- Higher Quality Content
- 60% Fewer Hallucinations
Browse by: Latest US Patents, China's latest patents, Technical Efficacy Thesaurus, Application Domain, Technology Topic, Popular Technical Reports.
© 2025 PatSnap. All rights reserved.Legal|Privacy policy|Modern Slavery Act Transparency Statement|Sitemap|About US| Contact US: help@patsnap.com