Method for producing potassium nitrate by chilisaltpeter ore transformation process
A technology of sodium nitrate ore and potassium nitrate, which is applied in the field of producing potassium nitrate by using the conversion method of sodium nitrate ore, can solve the problems of large investment in the construction of beach-dried salt fields, large process water consumption, and low concentration of sodium nitrate, so as to save investment and simplify Process flow and high energy efficiency utilization
- Summary
- Abstract
- Description
- Claims
- Application Information
AI Technical Summary
Problems solved by technology
Method used
Image
Examples
Embodiment 1
[0023] The method for producing sodium nitrate with sodium nitrate ore, its refinement processing step is
[0024] 1. Ore crushing: Sodium nitrate ore is crushed with a jaw crusher, and the particles with a particle size of ≤2cm are screened and loaded into the leaching tank.
[0025] 2. Five-stage countercurrent circulation leaching: the washing mother liquor enters five-stage countercurrent circulation leaching, the first stage is the fifth leaching of ore, the second stage is the fourth leaching of ore, and so on, the temperature of the leaching solution is graded As the concentration increases, the concentration of the washing liquid also increases step by step, and the leaching completion liquid is obtained. The leaching time of each level is 10h.
[0026] 3. Three-stage washing: use 0.5 times the weight of the ore to wash the ore after five-stage leaching step by step, and the washing sequence is the first stage, the second stage, and the third stage. Wherein the first...
Embodiment 2
[0040] The present embodiment has the same processing steps as Embodiment 1, and only differs in some process parameters, as follows:
[0041] 1. Ore crushing: crush the ore to particles with a particle size of ≤2cm, and put them into the leaching tank.
[0042] 2. Five-stage countercurrent circulation leaching: the washing mother liquor enters five-stage countercurrent circulation leaching, the first stage is the fifth leaching of ore, the second stage is the fourth leaching of ore, and so on, the leaching temperature is at room temperature ~ 50°C and increasing step by step, the concentration of the washing solution also increases step by step, and the leaching complete solution is obtained. The leaching time of each level is 8h.
[0043] 3. Three-stage washing: use 0.5 times the weight of the ore to carry out step-by-step washing, and the washing sequence is the first stage, the second stage, and the third stage. Wherein the first stage is the third washing of the ore, the ...
PUM
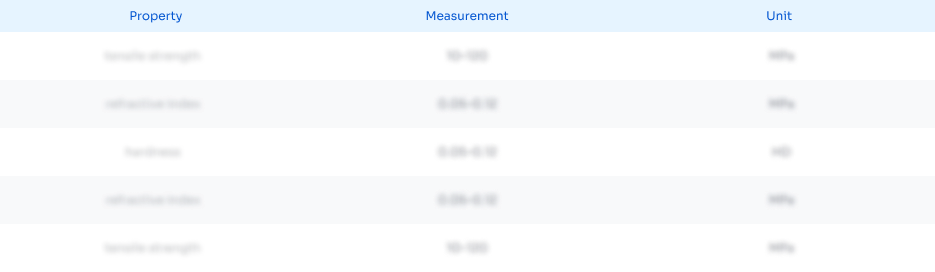
Abstract
Description
Claims
Application Information

- R&D
- Intellectual Property
- Life Sciences
- Materials
- Tech Scout
- Unparalleled Data Quality
- Higher Quality Content
- 60% Fewer Hallucinations
Browse by: Latest US Patents, China's latest patents, Technical Efficacy Thesaurus, Application Domain, Technology Topic, Popular Technical Reports.
© 2025 PatSnap. All rights reserved.Legal|Privacy policy|Modern Slavery Act Transparency Statement|Sitemap|About US| Contact US: help@patsnap.com