Method of preparing novel gradient functional material fine blanking die based on laser fusing-covering forming technique
A gradient functional material and laser cladding molding technology, applied in the field of mold manufacturing, can solve the problems of not involving fine blanking mold manufacturing, gradient structure can not be accurately controlled, etc., to achieve the effect of eliminating component segregation, short manufacturing cycle, and improving mechanical properties
- Summary
- Abstract
- Description
- Claims
- Application Information
AI Technical Summary
Problems solved by technology
Method used
Image
Examples
Embodiment Construction
[0016] In order to make the technical means, creative features, goals and effects achieved by the present invention easy to understand, the present invention will be further described below in conjunction with specific illustrations.
[0017] A method for manufacturing a fine-blanking die of a novel graded functional material based on laser cladding molding technology, comprising the following steps: figure 1 As shown, first adopt CO 2 Laser 1 uses a high-energy laser beam to locally melt the surface of the base metal to form a molten pool. During the processing process, the numerical control system can be used to control the workbench to scan back and forth according to the route given by the CAD model, and then the deposition substrate can be clad line by line and layer by layer. Stack up functional three-dimensional metal solid parts of any shape; then feed the metal raw material into the molten pool to form multiple layers of new metal layers that are metallurgically combi...
PUM
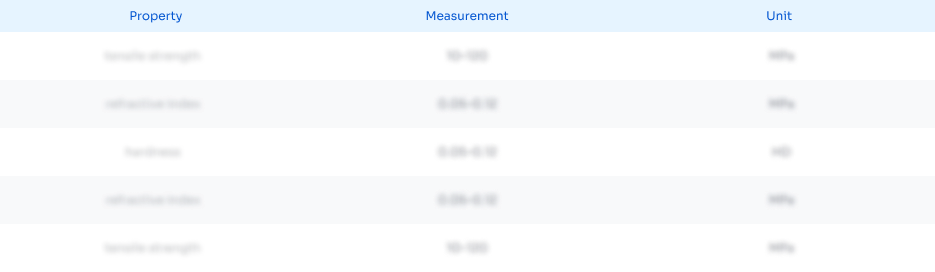
Abstract
Description
Claims
Application Information

- Generate Ideas
- Intellectual Property
- Life Sciences
- Materials
- Tech Scout
- Unparalleled Data Quality
- Higher Quality Content
- 60% Fewer Hallucinations
Browse by: Latest US Patents, China's latest patents, Technical Efficacy Thesaurus, Application Domain, Technology Topic, Popular Technical Reports.
© 2025 PatSnap. All rights reserved.Legal|Privacy policy|Modern Slavery Act Transparency Statement|Sitemap|About US| Contact US: help@patsnap.com