Crash resistant composite material and method for producing the same
A technology of composite materials and gravel materials, which is applied in the field of anti-collision composite materials and the preparation of anti-collision composite materials, can solve the problems of concrete gate walls not being resistant to collision and friction, and achieve excellent comprehensive performance, high hardness, and improved hardness.
- Summary
- Abstract
- Description
- Claims
- Application Information
AI Technical Summary
Problems solved by technology
Method used
Image
Examples
Embodiment 1
[0030] The anti-collision composite material comprises 100 parts by weight of modified epoxy resin, 20 parts by weight of active toughening agent, 0.04 parts by weight of surfactant, 40 parts by weight of fly ash and silica fume, and 30 parts by weight of gravel material;
[0031] The preparation method of anti-collision composite material of the present invention is:
[0032] EPIKOTE produced by British Shell TM Put Resin 828K epoxy resin, acrylic acid, fumaric acid, methacrylic acid, carboxy-terminated nitrile liquid rubber, p-phenol, tertiary amine, and quaternary ammonium salt into the reaction kettle at a ratio of 15:1, mix evenly, and slowly heat up to 150°C , after the basic reaction is complete, keep warm for 1.5 hours to make the reaction constant; then cool down to about 120°C, add styrene, methyl methacrylate (the addition of the diluent is 30% of the total amount of epoxy resin and modifier %, fully stirred and diluted; finally cooled to room temperature and filt...
Embodiment 2
[0040] The anti-collision composite material comprises 100 parts by weight of modified epoxy resin, 25 parts by weight of active toughening agent, 0.03 parts by weight of surfactant, 35 parts by weight of silica fume and quartz powder, and 20 parts by weight of gravel material;
[0041] The preparation method of anti-collision composite material of the present invention is:
[0042] EPIKOTE produced by British Shell TM Resin 828K epoxy resin and acrylic acid, fumaric acid, sebacic acid, carboxy-terminated nitrile liquid rubber, p-phenol, tertiary amine, and quaternary ammonium salt are put into the reaction kettle at a ratio of 10:1, mixed evenly, and slowly heated up to 160°C, after the basic reaction is complete, keep warm for 1 hour to make the reaction constant; then cool down to about 120°C, add styrene, methyl methacrylate (the amount of diluent added is the total amount of epoxy resin and modifier 40% of the amount), fully stirred and diluted; cooled to room temperatu...
Embodiment 3
[0049] The anti-collision composite material comprises 100 parts by weight of modified epoxy resin, 15 parts by weight of active toughening agent, 0.05 parts by weight of surfactant, 20 parts by weight of fly ash, silica fume and quartz powder, and 40 parts by weight of gravel material;
[0050] The preparation method of anti-collision composite material of the present invention is:
[0051] EPIKOTE produced by British Shell TM Resin 828K epoxy resin and acrylic acid, fumaric acid, adipic acid, amino-terminated nitrile liquid rubber, p-phenol, tertiary amine, and quaternary ammonium salt are put into the reaction kettle at a ratio of 20:1, mixed evenly, and slowly heated up to 140°C, after the basic reaction is complete, keep warm for 2 hours to make the reaction constant; then cool down to about 120°C, add styrene, methyl methacrylate (the addition of the diluent is the total amount of epoxy resin and modifier 50% of the amount), fully stirred and diluted; cooled to room te...
PUM
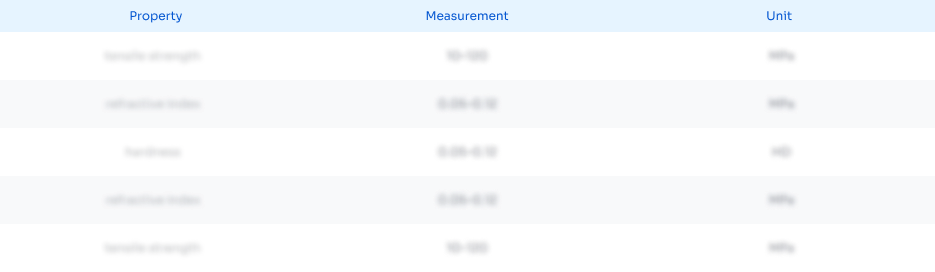
Abstract
Description
Claims
Application Information

- R&D
- Intellectual Property
- Life Sciences
- Materials
- Tech Scout
- Unparalleled Data Quality
- Higher Quality Content
- 60% Fewer Hallucinations
Browse by: Latest US Patents, China's latest patents, Technical Efficacy Thesaurus, Application Domain, Technology Topic, Popular Technical Reports.
© 2025 PatSnap. All rights reserved.Legal|Privacy policy|Modern Slavery Act Transparency Statement|Sitemap|About US| Contact US: help@patsnap.com