Method for manufacturing plant fibre composite wall plate
A technology of composite walls and plant fibers, which is applied in the direction of manufacturing tools, flat products, pretreatment of molding materials, etc., can solve the problems of uneven distribution of raw materials, high consumption, and high manufacturing costs, and achieves simple process and low manufacturing costs. , light weight effect
- Summary
- Abstract
- Description
- Claims
- Application Information
AI Technical Summary
Problems solved by technology
Method used
Image
Examples
specific Embodiment approach 1
[0008] Specific Embodiment 1: In this embodiment, the manufacturing method of plant fiber composite wall panels is realized through the following steps: 1. Clean and cut the crop stalks to a length of 3 to 6 cm, crush them with a fiber re-shredder, and sieve out dust and Obtain 40-80 mesh crop straw scraps after bulking; 2. Dry the crop straw scraps at 80-120°C until the moisture content is 3-8%; 3. Add the dried crop straw scraps to In the glue mixing machine, apply an adhesive accounting for 10-16% of the weight of crop straw scraps and stir evenly; 4. Add 1-9% of the weight of crop straw scraps to the glued crop straw scraps. 5. Pre-press the paved slab for 60-150s at room temperature and 4-8MPa; 6. Hot-press at 150-180°C and 6-12MPa 10-17min, then cut the edge after cooling at room temperature; the obtained density is 0.4-0.6cm 3 / g crop straw particle board; Seventh, the crop straw particle board and polystyrene board are layered and compounded, and the surface is pasted...
specific Embodiment approach 2
[0009] Embodiment 2: This embodiment is different from Embodiment 1 in that in step 1, the crop stalk is one of wheat straw, rice straw, corn stalk and cotton firewood or a combination of several of them. Others are the same as in the first embodiment.
[0010] In this embodiment, when the crop straws are a composition, various crop straws can be mixed in any ratio.
specific Embodiment approach 3
[0011] Embodiment 3: This embodiment is different from Embodiment 1 in that in step 2, the crop straw fragments are dried to a moisture content of 4-7%. Others are the same as in the first embodiment.
PUM
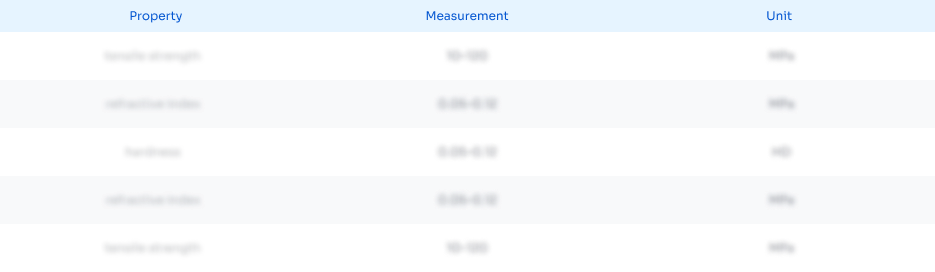
Abstract
Description
Claims
Application Information

- R&D Engineer
- R&D Manager
- IP Professional
- Industry Leading Data Capabilities
- Powerful AI technology
- Patent DNA Extraction
Browse by: Latest US Patents, China's latest patents, Technical Efficacy Thesaurus, Application Domain, Technology Topic, Popular Technical Reports.
© 2024 PatSnap. All rights reserved.Legal|Privacy policy|Modern Slavery Act Transparency Statement|Sitemap|About US| Contact US: help@patsnap.com