Vanadium iron spraying powder refining technique
A powder spraying and ferrovanadium technology is applied in the field of vanadium smelting, which can solve the problems of more losses than gains, unfavorable sustainable development, increased powder spraying and refining costs, etc., and achieves the effects of improving the recovery rate of vanadium, improving the reaction kinetic conditions and reducing the production cost.
- Summary
- Abstract
- Description
- Claims
- Application Information
AI Technical Summary
Problems solved by technology
Method used
Examples
Embodiment 1
[0011] 1. Preparation of FeV80 smelting main charge: TV 64.1% V 2 o 3 1000kg, 98.3% V 2 o 5 2000kg, aluminum powder 1350kg, iron powder 330kg; prepare 90 kg of refined reduction powder, wherein aluminum powder 77% iron powder 23%, mix evenly and put into powder tank.
[0012] 2. Use the electric aluminothermic method to smelt ferrovanadium. After the main charge fully completes the aluminothermic reaction and the alloy and slag are separated, power off to lift the electrode, rotate the furnace body, and then insert the nozzle of the spray gun into the slag layer by 450-500mm. Spray the refined and reduced powder into the slag layer within 80 to 120 seconds, and the pressure of the injected reduced powder gas is 0.3Mpa to 0.5Mpa; after the reduced powder and slag are impacted by the blowing airflow and the furnace body is rotated and stirred , lift the spray gun, and stop the furnace rotation at the same time, then insert the electrode and continue heating and melting for 20...
Embodiment 2
[0015] 1. Preparation of FeV80 smelting main charge: TV 64.1% V 2 o 3 2000kg, 98.3% V 2 o 5 1000kg, aluminum powder 1330kg, iron powder 370kg; prepare 80 kg of refined reduction powder, wherein aluminum powder 75% iron powder 25%, mix evenly and put into powder tank.
[0016] 2. Use the electric aluminothermic method to smelt ferrovanadium. After the main charge fully completes the aluminothermic reaction and the alloy and slag are separated, power off to lift the electrode, rotate the furnace body, and then insert the nozzle of the spray gun into the slag layer by 450-500mm. Spray the refined and reduced powder into the slag layer within 80 to 120 seconds, and the pressure of the injected reduced powder gas is 0.3Mpa to 0.5Mpa; after the reduced powder and slag are impacted by the blowing airflow and the furnace body is rotated and stirred , lift the spray gun, and stop the furnace rotation at the same time, then insert the electrode and continue heating and melting for 20...
Embodiment 3
[0019] 1. Preparation of FeV50 smelting main charge: TV63.9% V 2 o 3 1400kg, 96.0% V 2 o 5 1000kg, aluminum powder 1110kg, iron powder 1240kg; prepare 80 kg of refined reduction powder, wherein aluminum powder 75% iron powder 25%, mix evenly and put into the powder tank.
[0020] 2. Use the electric aluminothermic method to smelt ferrovanadium. After the main charge fully completes the aluminothermic reaction and the alloy and slag are separated, power off to lift the electrode, rotate the furnace body, and then insert the nozzle of the spray gun into the slag layer by 450-500mm. Spray the refined and reduced powder into the slag layer within 80 to 120 seconds, and the pressure of the injected reduced powder gas is 0.3Mpa to 0.5Mpa; after the reduced powder and slag are impacted by the blowing airflow and the furnace body is rotated and stirred , lift the spray gun, and stop the furnace rotation at the same time, then insert the electrode and continue heating and melting fo...
PUM
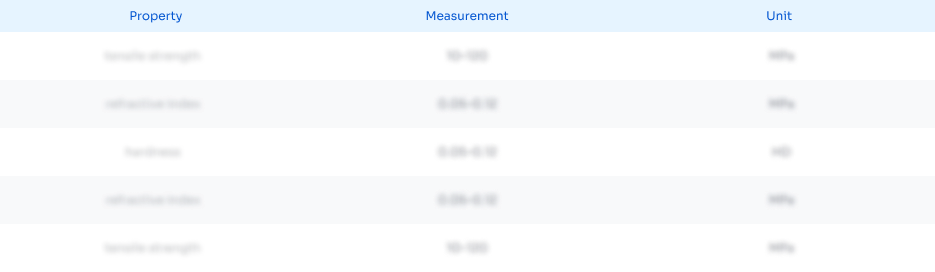
Abstract
Description
Claims
Application Information

- R&D
- Intellectual Property
- Life Sciences
- Materials
- Tech Scout
- Unparalleled Data Quality
- Higher Quality Content
- 60% Fewer Hallucinations
Browse by: Latest US Patents, China's latest patents, Technical Efficacy Thesaurus, Application Domain, Technology Topic, Popular Technical Reports.
© 2025 PatSnap. All rights reserved.Legal|Privacy policy|Modern Slavery Act Transparency Statement|Sitemap|About US| Contact US: help@patsnap.com