Refining method for efficiently smelting low-sulfur steel with low cost
A low-cost, low-sulfur steel technology, applied in the field of smelting low-sulfur steel, can solve the problems of long refining cycle, large alloy consumption, and difficulty in melting slag, so as to save refining cost, quickly transform slag into slag, and shorten smelting time Effect
- Summary
- Abstract
- Description
- Claims
- Application Information
AI Technical Summary
Problems solved by technology
Method used
Examples
Embodiment 1
[0034] In this embodiment, the composition of desulfurization synthetic slag is: refining slag 65%, manganese ore 25%, anthracite 5%, lime 5%.
[0035] This implementation is aimed at the method of smelting low-sulfur steel in 50t LF refining ladle. Before tapping the electric furnace, add 600kg of desulfurized synthetic slag into the refining ladle and bake it together with the ladle; when tapping the electric furnace, take steel sample 1 and measure the temperature, add the molten steel from the electric furnace to the ladle, and the ladle enters the refining station, before starting refining Take steel sample 2 and measure the temperature; LF starts to heat up and refine, and the bottom blowing intensity is 0.006Nm 3 / t min, target temperature 1600℃, add 40kg aluminum, 100kg silicon manganese for deoxidation alloying, take steel sample 3 after smelting for 5 minutes and measure temperature; then add 1400kg desulfurization synthetic slag, SiC 100kg, adjust the bottom blowing...
Embodiment 2
[0039] In this embodiment, the composition of desulfurization synthetic slag is: refining slag 65%, manganese ore 25%, anthracite 5%, lime 5%.
[0040] This implementation is aimed at the method of smelting low-sulfur steel in 50t LF refining ladle. Before tapping the electric furnace, add 800kg of desulfurized synthetic slag into the refining ladle and bake it together with the ladle; when tapping the electric furnace, take steel sample 1 and measure the temperature, add molten steel from the electric furnace to the ladle, and the ladle enters the refining station, before starting refining Take steel sample 2 and measure the temperature; LF starts to heat up and refine, and the bottom blowing intensity is 0.006Nm 3 / t min, the target temperature is 1600℃, add 40kg aluminum, 100kg silicomanganese for deoxidation alloying, take steel sample 3 after smelting for 5 minutes and measure the temperature; then add 1200kg of desulfurization synthetic slag and 100kg of SiC, and adjust ...
Embodiment 3
[0044] In this embodiment, the composition of desulfurization synthetic slag is: refining slag 65%, manganese ore 25%, anthracite 5%, lime 5%.
[0045] This implementation is aimed at the method of smelting low-sulfur steel in 50t LF refining ladle. Before tapping the electric furnace, add 1000kg of desulfurized synthetic slag into the refining ladle and bake it together with the ladle; when tapping the electric furnace, take steel sample 1 and measure the temperature, add the molten steel from the electric furnace to the ladle, and the ladle enters the refining station, before starting the refining Take steel sample 2 and measure the temperature; LF starts to heat up and refine, and the bottom blowing intensity is 0.006Nm 3 / t min, the target temperature is 1600℃, add 40kg aluminum, 100kg silicomanganese for deoxidation alloying, take steel sample 3 after smelting for 5 minutes and measure the temperature; then add 1200kg of desulfurization synthetic slag and 100kg of SiC, an...
PUM
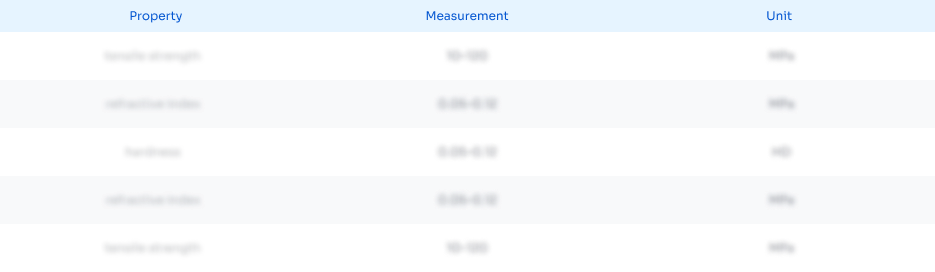
Abstract
Description
Claims
Application Information

- R&D
- Intellectual Property
- Life Sciences
- Materials
- Tech Scout
- Unparalleled Data Quality
- Higher Quality Content
- 60% Fewer Hallucinations
Browse by: Latest US Patents, China's latest patents, Technical Efficacy Thesaurus, Application Domain, Technology Topic, Popular Technical Reports.
© 2025 PatSnap. All rights reserved.Legal|Privacy policy|Modern Slavery Act Transparency Statement|Sitemap|About US| Contact US: help@patsnap.com