Method for reducing residual vanadium content in ferrovanadium smelting slag
A smelting furnace and slag technology, applied in the field of metallurgy, can solve problems such as insufficient reduction of slag, poor fluidity of slag, deterioration of mass transfer conditions, etc., to improve reaction kinetics conditions, increase settling time, and significant social and economic benefits Effect
- Summary
- Abstract
- Description
- Claims
- Application Information
AI Technical Summary
Problems solved by technology
Method used
Examples
Embodiment 1
[0032] The arc starting material in this embodiment is 595kgV 2 o 5 (grade 98.0%) is mixed with aluminum powder, the aluminum ratio is 1.02, and 65kg of iron pellets and 69kg of lime are added in addition. The refining material in the present embodiment is 150kg lime and 130kg aluminum powder.
[0033] The raw materials vanadium oxide, aluminum, iron and lime that meet the production requirements are mixed according to certain requirements. The overall aluminum distribution coefficient is 1.02, and the aluminum distribution coefficient ratio of the first batch of materials, the second batch of materials and the third batch of materials is 0.98:1.0 :1.02. The first batch of material is 805kg V 2 o 3 (Containing 63.1% of vanadium) with aluminum powder, with an aluminum ratio of 0.98, plus 103kg of iron pellets and 70kg of lime; the second batch of materials is 1618kg V 2 o 3 (containing 63.2% of vanadium) with aluminum powder, with an aluminum ratio of 1.0, plus 205kg of iro...
Embodiment 2
[0036] The arc starting material in this embodiment is 576kg V 2 o 5 (grade 98.0%) is mixed with aluminum powder, the aluminum ratio is 1.02, and 65kg of iron pellets and 70kg of lime are added in addition. The refining material in the present embodiment is 150kg lime and 130kg aluminum powder.
[0037] The raw materials vanadium oxide, aluminum, iron and lime that meet the production requirements are mixed according to certain requirements. The overall aluminum distribution coefficient is 1.02, and the aluminum distribution coefficient ratio of the first batch of materials, the second batch of materials and the third batch of materials is 0.97:1.0 :1.03. The first batch of material is 784kg V 2 o 3 (Containing vanadium 62.9%) with aluminum powder, with an aluminum ratio of 0.97, plus 100kg of iron pellets and 71kg of lime; the second batch of materials is 1558kg V 2 o 3 (containing 62.9% of vanadium) with aluminum powder, with an aluminum ratio of 1.0, plus 200kg of iro...
Embodiment 3
[0040] The arc starting material in this embodiment is 601kg of V 2 o 5 (grade 98.0%) is mixed with aluminum powder, the aluminum ratio is 1.02, and 65kg of iron pellets and 70kg of lime are added in addition. The refining material in the present embodiment is 150kg lime and 130kg aluminum powder.
[0041] The raw materials vanadium oxide, aluminum, iron and lime that meet the production requirements are mixed according to certain requirements. The overall aluminum distribution coefficient is 1.02, and the aluminum distribution coefficient ratio of the first batch of materials, the second batch of materials and the third batch of materials is 0.96:1.0 :1.04. The first batch of material is 799kg V 2 o 3 (Containing 63.2% of vanadium) with aluminum powder, with an aluminum ratio of 0.96, plus 103kg of iron pellets and 69kg of lime; the second batch of materials is 1612kg V 2 o 3 (containing 62.4% of vanadium) with aluminum powder, with an aluminum ratio of 1.0, plus 200kg ...
PUM
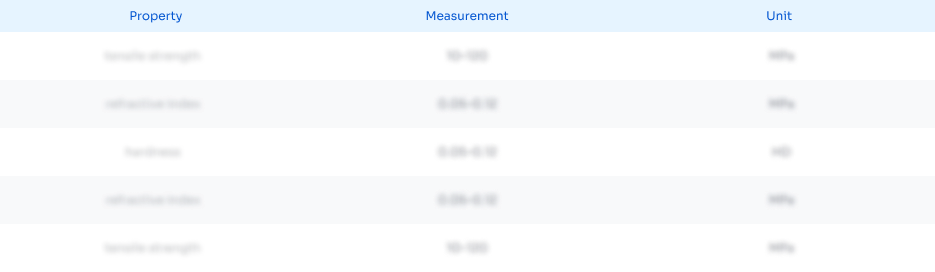
Abstract
Description
Claims
Application Information

- R&D
- Intellectual Property
- Life Sciences
- Materials
- Tech Scout
- Unparalleled Data Quality
- Higher Quality Content
- 60% Fewer Hallucinations
Browse by: Latest US Patents, China's latest patents, Technical Efficacy Thesaurus, Application Domain, Technology Topic, Popular Technical Reports.
© 2025 PatSnap. All rights reserved.Legal|Privacy policy|Modern Slavery Act Transparency Statement|Sitemap|About US| Contact US: help@patsnap.com