Non-pressure braze welding method for ZrO2 ceramic and stainless steel or Al2O3 ceramic
A stainless steel and brazing technology, applied in the field of pressureless brazing connection between ZrO2 ceramics and stainless steel or Al2O3 ceramics, can solve the problems of difficult connection between zirconia and stainless steel, difficult to eliminate welding stress, large elastic modulus of stainless steel, etc. The effect of high temperature performance, welding stress relief, and simple preparation process
- Summary
- Abstract
- Description
- Claims
- Application Information
AI Technical Summary
Problems solved by technology
Method used
Image
Examples
Embodiment 1
[0029] As shown in Figure 2, a ZrO 2 Method for pressureless brazing of ceramics and stainless steel.
[0030] 1. Preparation of zirconia ceramic parts:
[0031] (1) Cleaning treatment of zirconia ceramics: the zirconia ceramic piece 1 used is molded, sintered in an air furnace at 1550°C for 2h, and contains 3mol% Y 2 o 3 Partially stabilized zirconia ceramics with a size of Φ17×6mm. After rigorous cleaning of the zirconia ceramic part 1 (sequentially boiled with dilute alkali, rinsed with a large amount of tap water, ultrasonically cleaned with acetone, and boiled with distilled water), it is then dried in an oven at 80°C for 3 hours.
[0032] (2)TiH 2 Preparation of ointment: first commercially available TiH 2 Powder, add absolute ethanol, roll and mix ball mill for 80h, dry, the median diameter is 2.785μm according to the particle size distribution test, pass through a 200 mesh sieve, and then put in the finely ground TiH 2 Add ethylene oxalate to the glass bottle of ...
Embodiment 2
[0042] As shown in Figure 3, another ZrO 2 Method for pressureless brazing of ceramics and stainless steel.
[0043] 1. Preparation of zirconia ceramic parts:
[0044] (1) Cleaning treatment of zirconia ceramics: After the commercially available zirconia ceramic tube 11 is strictly cleaned (in turn, washed with dilute alkali, rinsed with a large amount of tap water, ultrasonically cleaned with acetone, boiled with distilled water), then placed in an oven for 80 ℃×3h drying treatment.
[0045] Other methods in this step are the same as (2), (3), (4) in embodiment 1-. where TiH 2 The paste is coated on the two ends of the zirconia ceramic tube 11 with a height of 4 cm side and end faces to form two TiH 2 Coating4.
[0046] 2. Treatment of stainless steel: The stainless steel used is processed into stainless steel welded pipe 12 and stainless steel welded cover 15 with holes respectively, and nickel-plated on the required brazing surface, wherein, the brazing end surface of ...
Embodiment 3
[0050] a ZrO 2 Ceramic and Al 2 o 3 Ceramic pressureless brazing method
[0051] 1. Preparation of zirconia ceramic parts. This step technology is with embodiment 1.
[0052] 2. Metallization treatment on the surface of alumina ceramics:
[0053] (1) Preparation and treatment of alumina ceramics: the alumina ceramics used are molded by molding technology, sintered in an air furnace at 1550 ° C × 2h, containing 95wt% Al 2 o 3 , 2.5wt% SiO 2 And 2.5wt% MgO alumina ceramic piece, the size is Φ17×6mm. The brazed surface of the final sintered alumina ceramic piece is polished, cleaned (in turn, washed with dilute alkali, rinsed with water, ultrasonically cleaned with acetone, and boiled with distilled water), and then dried.
[0054] (2) Mo-Mn sintering metallization: Coat the Mo-Mn metal paste adjusted with Mo-Mn composite powder, collodion solution and oxalate on the brazing surface of the alumina ceramic sheet treated in the previous step, Paste adjustment method is the...
PUM
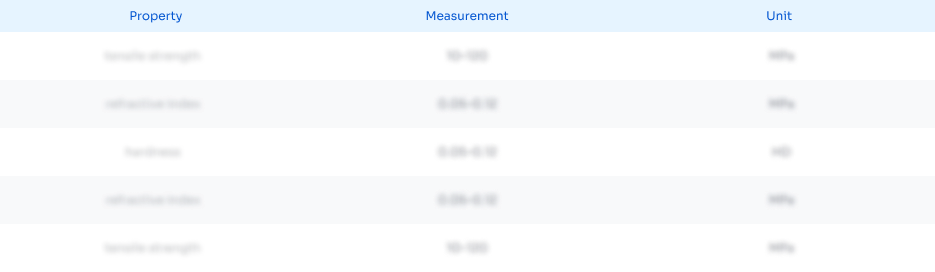
Abstract
Description
Claims
Application Information

- R&D Engineer
- R&D Manager
- IP Professional
- Industry Leading Data Capabilities
- Powerful AI technology
- Patent DNA Extraction
Browse by: Latest US Patents, China's latest patents, Technical Efficacy Thesaurus, Application Domain, Technology Topic, Popular Technical Reports.
© 2024 PatSnap. All rights reserved.Legal|Privacy policy|Modern Slavery Act Transparency Statement|Sitemap|About US| Contact US: help@patsnap.com