Temperature gradient controllable wafer front-drying method and its hot plate type front drying device
A temperature gradient and wafer technology, applied in the direction of electrical components, semiconductor/solid-state device manufacturing, circuits, etc., can solve problems such as the inability to directly control the wafer temperature, and achieve excellent photolithographic effects, high integration, and excellent film properties.
- Summary
- Abstract
- Description
- Claims
- Application Information
AI Technical Summary
Problems solved by technology
Method used
Image
Examples
Embodiment Construction
[0043] The present invention will be described in further detail below in conjunction with the accompanying drawings.
[0044] As shown in Figures 2 and 9, in the semiconductor chip manufacturing process, the hot plate type pre-baking device used for pre-baking after coating the photoresist on the wafer includes a hot plate body 4, a heater 11 and a temperature detection device 9 1. The body of furnace with four walls surrounded by the frame has three vertical needle rods for supporting the wafer 12, and also includes a lift mechanism (such as screw mandrel 5, motor 7 and encoder 6) and servo driver 8 etc., wherein: be provided with heater (can be rod-shaped or sheet structure) and chip temperature detecting device 9 (such as: Pt100 thermal resistance or thermoelectric coupler) in the hot plate body, respectively with heat Disc temperature controller 10 (prior art, commercially available) is electrically connected; Ejector pin 3 is located on the heating disc body 4, is connec...
PUM
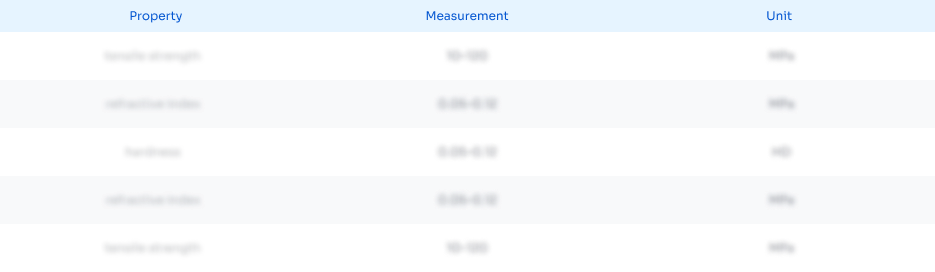
Abstract
Description
Claims
Application Information

- R&D Engineer
- R&D Manager
- IP Professional
- Industry Leading Data Capabilities
- Powerful AI technology
- Patent DNA Extraction
Browse by: Latest US Patents, China's latest patents, Technical Efficacy Thesaurus, Application Domain, Technology Topic, Popular Technical Reports.
© 2024 PatSnap. All rights reserved.Legal|Privacy policy|Modern Slavery Act Transparency Statement|Sitemap|About US| Contact US: help@patsnap.com