Fluorinated polyesters with low surface energy and preparation method thereof
A low surface energy, fluorine-containing polyester technology, applied in the field of polymer materials, can solve problems such as inability to melt, complicated construction process, and poor adhesion
- Summary
- Abstract
- Description
- Claims
- Application Information
AI Technical Summary
Problems solved by technology
Method used
Image
Examples
Embodiment 1
[0034] Synthesis of N-hydroxyethyl perfluorooctylamide-terminated polybutylene isophthalate
[0035] Preheat the reaction system to 110°C, add 0.05mol dimethyl isophthalate, 0.047mol 1,4-butanediol, 0.003mol N-hydroxyethyl perfluorooctylamide and 0.1% (wt% )Tetrabutyl titanate. React at 160-180°C for 1 hour. Start vacuuming, and heat up at the same time, at a temperature of 200-215° C., a vacuum of 85 mmHg, and react for 1.5 hours. Vacuum degree rises to 14mmHg, raise reaction temperature at the same time, react between 240-248 ℃ for 1.5 hours, stop heating, wait for the temperature in the reaction bottle to drop below 100 ℃, stop vacuuming. Add 50ml of chloroform to the product to dissolve the heat, then filter it with suction, settle the filtrate with 500ml of ethanol, dry the obtained solid, and grind it to obtain a solid product. Yield: 86.5%. The reaction molecular formula is as follows (wherein x=y+z, y / x+y+z=0.03):
[0036]
[0037]
[0038]
[0039] Raise t...
Embodiment 3
[0044] Synthesis of N-hydroxyethyl perfluorooctylamide-terminated polybutylene isophthalate
[0045] Preheat the reaction system to 110°C, add 0.05mol dimethyl isophthalate, 0.044mol 1,3-propanediol, 0.006mol pentafluorooctyl alcohol, and 0.1% (wt%) iso-titanate together under stirring nitrogen Propyl ester. React at 160-180°C for 1 hour. Start vacuuming and heat up at the same time, at a temperature of 200-210° C. and a vacuum of 85 mmHg, react for 1.5 hours. Vacuum degree rises to 14mmHg, raise reaction temperature at the same time, react between 240-245 ℃ for 1.5 hours, stop heating, wait until the temperature in the reaction bottle drops below 100 ℃, stop vacuuming. Add 50ml of chloroform to the product to dissolve the heat, then filter it with suction, settle the filtrate with 500ml of ethanol, dry the obtained solid, and grind it to obtain a solid product. Yield: 88%. The reaction molecular formula is as follows (wherein x=y+z, y / x+y+z=0.06):
[0046]
[0047] ...
Embodiment 4
[0050] Synthesis of dodecafluoroheptanol-terminated polybutylene isophthalate
[0051] Preheat the reaction system to 110°C, add 0.05mol dimethyl isophthalate, 0.046mol 2,2-dimethyl-1,3 propanediol, 0.004mol N-hydroxyethyl perfluorodecylamide, and 0.1% (wt%) tetrabutyl titanate. React at 170-180°C for 1 hour. Start vacuuming, and heat up at the same time, at a temperature of 205-215° C., a vacuum of 100 mmHg, and react for 1.5 hours. The vacuum degree was raised to 15mmHg, and the reaction temperature was increased at the same time, and the reaction was between 240-248°C for 1.5 hours, and the heating was stopped. When the temperature in the reaction bottle dropped below 100°C, the vacuum was stopped. Add 50ml of chloroform to the product to dissolve the heat, then dissolve it with suction, settle the filtrate with 500ml of ethanol, dry the obtained solid, and grind it to obtain a solid product. Yield: 90%. The reaction molecular formula is as follows (wherein x=y+z, y / x+y...
PUM
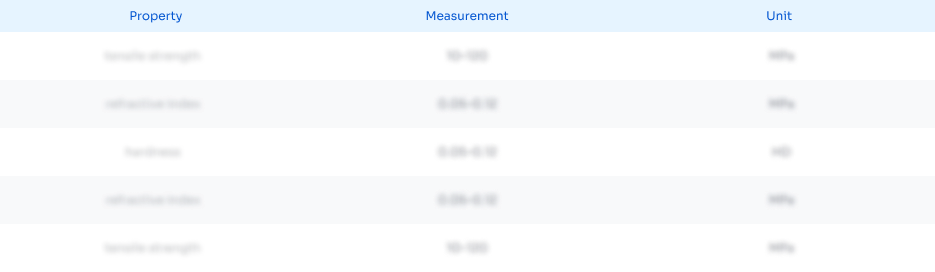
Abstract
Description
Claims
Application Information

- R&D
- Intellectual Property
- Life Sciences
- Materials
- Tech Scout
- Unparalleled Data Quality
- Higher Quality Content
- 60% Fewer Hallucinations
Browse by: Latest US Patents, China's latest patents, Technical Efficacy Thesaurus, Application Domain, Technology Topic, Popular Technical Reports.
© 2025 PatSnap. All rights reserved.Legal|Privacy policy|Modern Slavery Act Transparency Statement|Sitemap|About US| Contact US: help@patsnap.com