Equipment for manufacturing composite membrane filter of polytetrafluoroethylene
A polytetrafluoroethylene and composite filtration technology, which is applied in membrane technology, semi-permeable membrane separation, chemical instruments and methods, etc., can solve the problems of polytetrafluoroethylene microporous membrane not being self-supporting, unfavorable folding, and easy to deform. , to achieve the effects of high temperature sterilization physicochemical properties, adjustable compound parameters, and improved shrinkage and formability
- Summary
- Abstract
- Description
- Claims
- Application Information
AI Technical Summary
Problems solved by technology
Method used
Image
Examples
Embodiment 1
[0020] Embodiment 1: The manufacturing equipment used by polytetrafluoroethylene support composite filter membrane, its structure includes feeding and winding transmission device 1, pressing device 2 and control device 3, and control device 3 outputs control signal to feeding and winding transmission device 1 and Pressing device 2, feeding and winding transmission device 1 includes PTFE microporous membrane feeding roller 11, support material feeding roller 12, composite film winding roller 13, PTFE microporous membrane feeding and driving Roller 14, supporting material feeding drive roller 15 and composite film winding drive roller 16, pressing device 2 consists of a heating composite roller 21 and a cooling composite roller 22 opposite to the heating composite roller 21 arranged up and down to form, The surface of the heating composite roller 21 is coated with mirror stainless steel, and the cooling composite roller 22 is coated with a rubber outer layer outside the stainless...
Embodiment 2
[0021] Embodiment two: the manufacturing equipment that polytetrafluoroethylene support composite filter membrane is used, basic structure is identical with embodiment one, and difference is that pressing device 2 is made of two heating composite rolls 21 and with heating composite roll 21 relative Two cooling composite rollers 22 are arranged up and down to form.
[0022] In the above embodiments, the heating device 24 has no special requirements, and it can be an electric heating tube with oil, water, or gas as the medium, or gas heating, infrared heating, microwave heating, high-frequency heating, radiation heating, steam heating, etc., to heat The device 24 can be arranged inside the heating composite roller 21, also can be arranged outside the heating composite roller 21, or both inside and outside.
[0023] There is no special requirement for the cooling device 25, and water cooling or oil cooling can also be used.
[0024] The temperature measuring element thermocouple...
Embodiment 3
[0027]Embodiment 3: It is manufactured by laminating a polytetrafluoroethylene microporous filter membrane with a layer of polypropylene screen, adjusting the parameters of the equipment, and compounding: ① Feed the polytetrafluoroethylene microporous filter membrane The polytetrafluoroethylene microporous filter membrane on the roller and the polypropylene screen set on the supporting material feeding roller are conveyed to the pressing device composed of heating composite rollers and cooling composite rollers arranged up and down through the transmission control system In the process, make the polytetrafluoroethylene microporous filter membrane close to the heating composite roller, and make the polypropylene screen mesh close to the cooling composite roller; ②Through the heating device composed of 18 halogen lamps evenly arranged in the heating composite roller Make the surface temperature of the heating composite roller be 300°C, and make the surface temperature of the cool...
PUM
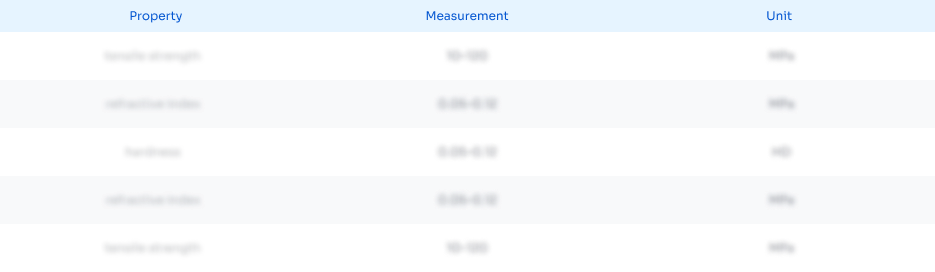
Abstract
Description
Claims
Application Information

- Generate Ideas
- Intellectual Property
- Life Sciences
- Materials
- Tech Scout
- Unparalleled Data Quality
- Higher Quality Content
- 60% Fewer Hallucinations
Browse by: Latest US Patents, China's latest patents, Technical Efficacy Thesaurus, Application Domain, Technology Topic, Popular Technical Reports.
© 2025 PatSnap. All rights reserved.Legal|Privacy policy|Modern Slavery Act Transparency Statement|Sitemap|About US| Contact US: help@patsnap.com