Prepn process of catalyst for selective oxidation of isobutene to produce methyl acraldehyde
A technology of methacrolein and selective oxidation, which is applied in the direction of oxidative preparation of carbonyl compounds, etc., can solve the problems of poisoning human body, environmental pollution, and high raw material prices, and achieve the effects of good dispersion effect, reduction of energy consumption, and improvement of preparation efficiency.
- Summary
- Abstract
- Description
- Claims
- Application Information
AI Technical Summary
Problems solved by technology
Method used
Examples
Embodiment 1
[0005] Embodiment 1: Catalyst preparation process parameter
[0006] In a certain amount of water at 50°C, dissolve a certain amount of ammonium molybdate to prepare solution A; in a certain volume of 15% nitric acid aqueous solution, dissolve a certain amount of bismuth nitrate, iron nitrate, cesium nitrate, potassium nitrate, and cobalt nitrate to prepare Solution B; at 50°C and under stirring conditions, add solution B dropwise to solution A to obtain a slurry. After adjusting the obtained slurry to a pH between 3-4 with ammonia water, age at 50°C for 10h, and in 110 12h at ℃, 3h at 200℃, and finally calcined at 500℃ for 3h.
[0007] The prepared catalyst is carried out on the normal pressure continuous fluidized bed micro-reaction, the stainless steel reaction tube is 300mm long, the inner diameter is 6mm, and the catalyst charge is 0.5ml. GHSV=9000h -1 , Isobutene content 6%. React between 320-400°C.
[0008] Response result:
[0009] Reaction temperature Isobutylene ...
Embodiment 2
[0015] Embodiment 2: Catalyst preparation process parameter
[0016] In a certain amount of water at 50°C, dissolve a certain amount of ammonium molybdate to prepare solution A; in a certain volume of 15% nitric acid aqueous solution, dissolve a certain amount of bismuth nitrate, iron nitrate, cesium nitrate, potassium nitrate, and cobalt nitrate to prepare solution B; at 50°C and under stirring conditions, add solution B dropwise to solution A to obtain a slurry. After adjusting the obtained slurry to a pH between 3-4 with ammonia water, use an ultrasonic oscillator at 50°C to vibrate 1h, dried at 110°C for 12h, dried at 200°C for 3h, and finally calcined at 500°C for 3h,
[0017] The prepared catalyst is carried out on the normal pressure continuous fluidized bed micro-reaction, the stainless steel reaction tube is 300mm long, the inner diameter is 6mm, and the catalyst charge is 0.5ml. GHSV=9000h -1 , Isobutene content 6%. React between 320-400°C.
[0018] Response resul...
Embodiment 3
[0025] Embodiment 3:. Catalyst Preparation Process Parameters
[0026] In a certain amount of water at 50°C, dissolve a certain amount of ammonium molybdate to prepare solution A; in a certain volume of 15% nitric acid aqueous solution, dissolve a certain amount of bismuth nitrate, iron nitrate, cesium nitrate, potassium nitrate, and cobalt nitrate to prepare solution B; at 50°C and under stirring conditions, add solution B dropwise to solution A to obtain a slurry. After adjusting the obtained slurry to a pH between 3-4 with ammonia water, use an ultrasonic oscillator at 50°C to vibrate 1h, dry at 110°C for 12h, dry at 200°C for 3h, use microwave at 800w, heat for 1h.
[0027] The prepared catalyst is carried out on the normal pressure continuous fluidized bed micro-reaction, the stainless steel reaction tube is 300mm long, the inner diameter is 6mm, and the catalyst charge is 0.5ml. GHSV=9000h -1 , Isobutene content 6%. React between 320-400°C.
[0028] Response result: ...
PUM
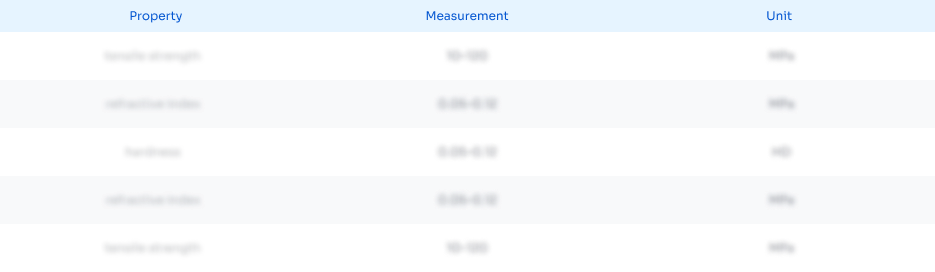
Abstract
Description
Claims
Application Information

- R&D Engineer
- R&D Manager
- IP Professional
- Industry Leading Data Capabilities
- Powerful AI technology
- Patent DNA Extraction
Browse by: Latest US Patents, China's latest patents, Technical Efficacy Thesaurus, Application Domain, Technology Topic, Popular Technical Reports.
© 2024 PatSnap. All rights reserved.Legal|Privacy policy|Modern Slavery Act Transparency Statement|Sitemap|About US| Contact US: help@patsnap.com