Method for preparing sheet alumina using coal series kaolin rock or flyash as raw material
A technology of flaky alumina and kaolinite, applied in chemical instruments and methods, inorganic chemistry, aluminum compounds, etc., can solve problems such as inability to achieve economical and effective iron removal, difficult control of alumina crystal form, and strict process conditions. Achieve the effects of low cost, large surface thickness ratio, and cheap and easy-to-obtain raw materials
- Summary
- Abstract
- Description
- Claims
- Application Information
AI Technical Summary
Problems solved by technology
Method used
Examples
Embodiment 1
[0017] 1) Coal series kaolinite is dried, pulverized, dry magnetically separated, then calcined at 550°C for 4 hours, mixed with sulfuric acid with a mass percentage concentration of 20%, and extracted at 250°C for 1 hour; filtered, that is get aluminum sulfate solution;
[0018] 2) adjusting the pH of the aluminum sulfate solution prepared in step 1) to 3 with sodium hydroxide, and filtering to obtain a purified aluminum sulfate solution;
[0019] 3) Evaporating and concentrating the purified aluminum sulfate solution obtained in step 2) to saturation, adding formic acid according to the ratio of aluminum: formic acid molar ratio of 1:50, cooling to room temperature, depositing aluminum sulfate, filtering to obtain refined aluminum sulfate flakes; Mother liquor recycling.
[0020] 4) Put the refined flaky aluminum sulfate obtained in step 3) into a calciner for pyrolysis, raise the temperature to 400°C at a rate of 2°C / min, and keep it warm for 1 hour; then raise the tempera...
Embodiment 2
[0022] 1) Dry the fly ash, pulverize it, dry magnetically separate it, then calcinate it at 850°C for 1 hour, mix it with nitric acid with a mass percentage concentration of 35%, and extract it at 100°C for 4 hours; centrifuge to obtain Aluminum nitrate solution;
[0023] 2) adjusting the pH of the aluminum nitrate solution prepared in step 1) to 5 with sodium bicarbonate, and centrifuging to obtain a purified aluminum nitrate solution;
[0024] 3) Evaporate and concentrate the purified aluminum nitrate solution obtained in step 2) to saturation, add acetic acid according to the ratio of aluminum:acetic acid molar ratio of 1:300, cool to room temperature, precipitate aluminum nitrate, and centrifuge to obtain refined flake aluminum nitrate ; Mother liquor recycling.
[0025] 4) Put the refined flaky aluminum nitrate obtained in step 3) into a calciner for pyrolysis, raise the temperature to 500°C at a rate of 20°C / min, and keep it warm for 2 hours; then raise the temperature ...
Embodiment 3
[0027] 1) Coal series kaolinite is dried, pulverized, dry magnetically separated, then calcined at 650°C for 3 hours, mixed with hydrochloric acid with a concentration of 30% by mass, and extracted at 125°C for 4 hours; filtered, that is Get aluminum chloride solution;
[0028] 2) adjusting the pH of the aluminum chloride solution prepared in step 1) to 5 with sodium carbonate, and centrifuging to obtain a purified aluminum chloride solution;
[0029] 3) Evaporating and concentrating the purified aluminum chloride solution obtained in step 2) to saturation, adding propionic acid in a ratio of 1:50 by the molar ratio of aluminum: propionic acid, cooling to room temperature, and separating out aluminum chloride, which is filtered or centrifuged, The refined flake aluminum chloride is obtained, and the mother liquor is recycled;
[0030] 4) Put the refined flake aluminum chloride obtained in step 3) into a calciner, raise the temperature to 500°C at a rate of 2°C / min, and keep i...
PUM
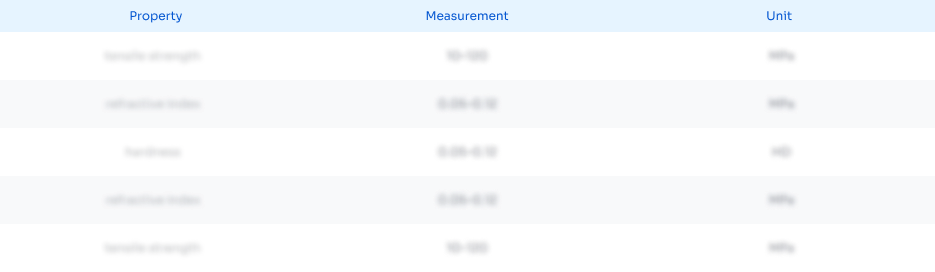
Abstract
Description
Claims
Application Information

- R&D Engineer
- R&D Manager
- IP Professional
- Industry Leading Data Capabilities
- Powerful AI technology
- Patent DNA Extraction
Browse by: Latest US Patents, China's latest patents, Technical Efficacy Thesaurus, Application Domain, Technology Topic, Popular Technical Reports.
© 2024 PatSnap. All rights reserved.Legal|Privacy policy|Modern Slavery Act Transparency Statement|Sitemap|About US| Contact US: help@patsnap.com