Process of producing iron alloy with low carbon and chromium
A ferrochrome alloy and production process technology, which is applied in the field of low-micro-carbon ferrochrome alloy production process, can solve the problems of long production cycle, high production cost, and many production links, and achieve production cost reduction, gas content reduction, and production process simplification Effect
- Summary
- Abstract
- Description
- Claims
- Application Information
AI Technical Summary
Problems solved by technology
Method used
Examples
Embodiment 1
[0014] Micro-carbon ferrochrome production:
[0015] 1) Weigh 1100Kg of high-carbon ferrochromium and put it into a 1000Kg intermediate frequency induction furnace, melt it, raise the temperature to above 1600°C, and pour it into the tank;
[0016] 2) Move the tank containing the high-carbon ferrochromium melt into the blowing station of the LAVOD furnace, install a dust cover on the mouth of the tank, turn on the bag dust removal fan, insert a Laval type oxygen spray gun into the tank to blow oxygen, and the oxygen gun 400-800mm away from the liquid level, connect the argon pipe from the bottom of the tank to blow argon, and the flow rate of the argon blowing is controlled at 50 liters / minute; Raise to 0.8mPa for blowing, add 50Kg chrome ore and 100-200Kg aluminum-calcium pre-melted slag at the same time, observe the flame at the mouth of the tank, and continue blowing for 5 minutes after the flame shrinks;
[0017] 3) Take out the oxygen lance, insert the Laval-type argon-s...
PUM
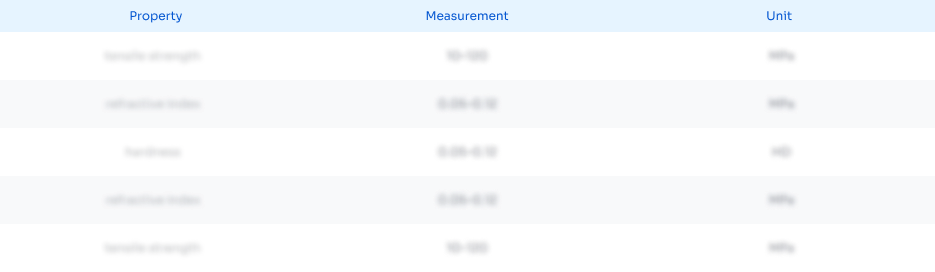
Abstract
Description
Claims
Application Information

- R&D
- Intellectual Property
- Life Sciences
- Materials
- Tech Scout
- Unparalleled Data Quality
- Higher Quality Content
- 60% Fewer Hallucinations
Browse by: Latest US Patents, China's latest patents, Technical Efficacy Thesaurus, Application Domain, Technology Topic, Popular Technical Reports.
© 2025 PatSnap. All rights reserved.Legal|Privacy policy|Modern Slavery Act Transparency Statement|Sitemap|About US| Contact US: help@patsnap.com