Microbiological degumming method for smartweed fibre
A technology of nettle fiber and degumming method, applied in the directions of microorganisms, microorganisms, biochemical equipment and methods, etc., can solve the problems of adverse effects on fiber quality, equipment corrosive environment, poor working conditions, etc., and achieves a reduction in the proportion of filaments and stems. , The effect of low residual glue rate and ease of processing conditions
- Summary
- Abstract
- Description
- Claims
- Application Information
AI Technical Summary
Problems solved by technology
Method used
Examples
Embodiment 1
[0029] Select different area distributions and different ages of liquor brewing cellars, isolate hundreds of strains of bacteria with strong ability to use grain raw materials from the fermented grains of cellars with different fermentation cycles, and inoculate them in 5g of yeast extract, CaCl 2 2H 2 O0.5g, sodium polypectate 10g, agar 14g, 1M NaOH 9mL, 0.2% bromothymol blue solution 12.5mL, add distilled water to 1000mL, sterilize with 0.1MPa wet pressure for 15min and pour the pectin medium plate , cultured upside down at 34°C for 3 days, select a culture plate whose colony growth and distribution are less than 300 colonies / plate, and the strains with the ability to degumming are selected from the culture plates with concave melting state and yellow change in the culture medium around the colonies, from which the colony growth The strains with strong ability and large pectin degradation ring should be stored at 4°C in 3g beef extract, 10g peptone, 5g sodium chloride, 1000m...
Embodiment 2
[0032] (1) Soaking treatment Put the nettle into water with a temperature of 25°C and soak it for 24 hours, then take it out;
[0033] (2) Degumming bacteria inoculation degumming The degumming bacteria screened and cultivated in embodiment 1 are made into a pH of 4.5 in the proportion of 5% of nettle weight before infiltration, and the bath ratio is a degumming solution of 1: 20, and then put into the infiltration The final nettles were degummed at a temperature of 36°C for 24 hours;
[0034] (3) Washing: the nettle fiber after the degumming is first washed with hot water at 70°C;
[0035](4) Refining put the washed nettle fiber into the lye with a bath ratio of 1:15 and boil for 1.5 hours, take it out and wash it with water, and remove the water by centrifugation. The lye used contains 0.2% sodium hydroxide by weight percentage , soap 0.2%;
[0036] (5) softening: put the dehydrated fiber into the softening solution prepared with an alkylbenzenesulfonate softening agent at...
Embodiment 3
[0041] (1) Soaking treatment Put the nettle into water with a temperature of 35°C and soak it for 36 hours, then take it out;
[0042] (2) degumming bacteria inoculation degumming The degumming bacteria screened and cultivated in embodiment 1 are made into a pH of 7.0 in the proportion of 10% of nettle weight before infiltration, and the bath ratio is 1: 30 degumming solution, then put into infiltration The final nettles were degummed at a temperature of 35°C for 36 hours;
[0043] (3) Washing The nettle fiber after the degumming is first washed with hot water at 80°C;
[0044] (4) Refining Putting the washed nettle fiber into the lye with a bath ratio of 1:40 and boiling it for 2.0 hours, taking it out and washing it with water, centrifuging to remove water, and containing 0.4% sodium hydroxide by weight percentage in the lye used , soap 0.3%;
[0045] (5) Softening: Put the dehydrated fiber into the softening solution prepared with fatty acid sulfate ester softening agent ...
PUM
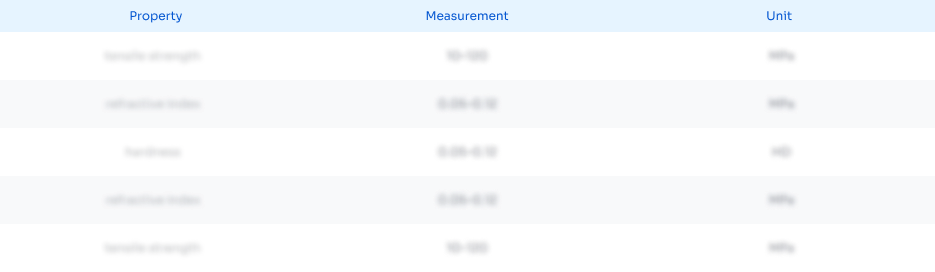
Abstract
Description
Claims
Application Information

- Generate Ideas
- Intellectual Property
- Life Sciences
- Materials
- Tech Scout
- Unparalleled Data Quality
- Higher Quality Content
- 60% Fewer Hallucinations
Browse by: Latest US Patents, China's latest patents, Technical Efficacy Thesaurus, Application Domain, Technology Topic, Popular Technical Reports.
© 2025 PatSnap. All rights reserved.Legal|Privacy policy|Modern Slavery Act Transparency Statement|Sitemap|About US| Contact US: help@patsnap.com