Method for nickel and cobalt recovery from laterite ores by reaction with concentrated acid and water leaching
A technology of water leaching and laterite ore, which is applied in the direction of improving process efficiency, etc., can solve the problems of low nickel extraction rate, not providing nickel better than iron selective dissolution, and not high, so as to achieve the effect of reducing production
- Summary
- Abstract
- Description
- Claims
- Application Information
AI Technical Summary
Problems solved by technology
Method used
Image
Examples
Embodiment 1
[0075]About 1 kg of saprolite ore was wet ground in a ball mill to about 100% passing through a 100 mesh screen. The ground slurry was filtered to produce a ground saprolite with a moisture content of 41%. 425.2 g of wet ground saprolite was mixed with 381.7 g of wet limonite ore to make 500 g of leach material with a limonite / saprolite ratio (on a dry solid basis) of 1:1.
[0076] Put the ore mixture into a 4.5-liter narrow-necked glass bottle. The bottles were rolled on a bottle rolling device at a slight angle to the horizontal at a speed of approximately 47 to 48 rpm. 312.5 g of 96% sulfuric acid was added to the ore mixture in the bottle over about 30 minutes. After all the acid has been added, the ore is mixed with the acid for about 30 minutes. At the end of mixing the ore and acid form a semi-fluid mass and the temperature rises to between about 70 and 100°C.
[0077] The bottle is removed from the rolling equipment and the mixture of acid and ore is allowed to age...
Embodiment 2
[0088] A 381.7 g sample of limonite ore was mixed with 317.7 g of crushed saprolite ore and 95 g of water in a 2 liter flat bottom glass beaker. Water was added to simulate the expected moisture content of the crude ore, it being recognized that the sample was slightly drier than it was in situ. 312.5 g of 96% sulfuric acid was added to the beaker over about 30 minutes. The acid was mixed with the ore using a stirrer at 60 rpm. The amount of acid added is sufficient so that the acid to ore ratio is about 600 kg H 2 SO 4 / ton of ore (calculated as dry product).
[0089] The semi-fluid mass of ore and acid was poured into shallow pans to age at room temperature for about 72 hours. A portion of the mixture was not recovered during this process, an estimated 13% of the mixture was not recovered on a gravimetric basis.
[0090] After the aging process, the acid / ore mixture, which has hardened significantly, is broken into chunks and transferred to small grinders. 300 g of wa...
Embodiment 3
[0100] This test was performed in a manner similar to Example 2 with the following differences. Limonite ore, crushed saprolite ore, water, acid and hematite seeds were used in amounts of 336.9 g, 280.3 g, 84 g, 275.8 g and 113 g during acid mixing and subsequent leaching, respectively. The proportions of ore, water and acid are the same as in Example 2.
[0101] After the ore is mixed with the acid, the mixture is transferred to shallow pans and matured for just 1 hour before being transferred to a grinder for wet grinding followed by water leaching. After 1 hour of aging, the mixture was still fluid and could be poured into a grinder. 1,776 g of leach slurry was prepared and leached in exactly the same way as in Example 2. The recovery of the acid / ore mixture was close to 96%.
[0102] The results of this test are given in Tables 6 and 7 below.
[0103] Table 6
[0104] time (h)
[Ni]g / L
[Fe]g / L
[H 2 SO 4 ]g / L
1
5.53...
PUM
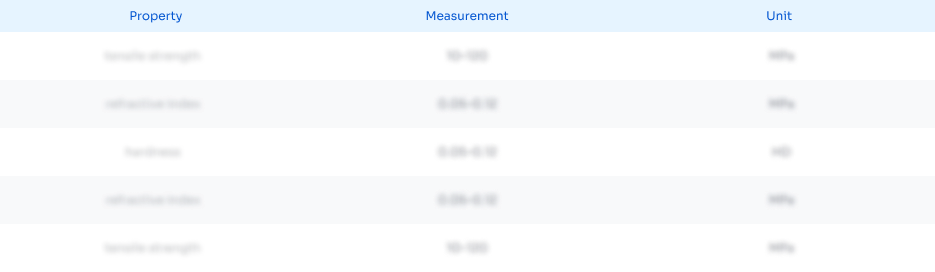
Abstract
Description
Claims
Application Information

- R&D
- Intellectual Property
- Life Sciences
- Materials
- Tech Scout
- Unparalleled Data Quality
- Higher Quality Content
- 60% Fewer Hallucinations
Browse by: Latest US Patents, China's latest patents, Technical Efficacy Thesaurus, Application Domain, Technology Topic, Popular Technical Reports.
© 2025 PatSnap. All rights reserved.Legal|Privacy policy|Modern Slavery Act Transparency Statement|Sitemap|About US| Contact US: help@patsnap.com