High performance pavement material of epoxy asphalt, preparation method and application
An epoxy asphalt and pavement material technology, which is applied to building thermal insulation materials, on-site coagulation pavement, roads, etc. The effect of improving bond strength and improving fatigue resistance
- Summary
- Abstract
- Description
- Claims
- Application Information
AI Technical Summary
Problems solved by technology
Method used
Examples
Embodiment 1
[0022] Material:
[0023] Part A: 480 parts of bitumen (Shell AH-70), 100 parts of modified oleic acid, 80 parts of modified ricinoleic acid, 4 parts of benzylamine, 4 parts of copolymer of ethylene oxide and propylene oxide.
[0024] Part B: Bisphenol A type epoxy resin.
[0025] Preparation:
[0026] Heat the asphalt to 100-130°C, add modified oleic acid and modified ricinoleic acid into the asphalt, stir and mix, then transfer to a colloid mill for high-speed shearing to disperse evenly, the shearing mixing time is 60 minutes, and then add Benzylamine as an accelerator and a copolymer of ethylene oxide and propylene oxide as a defoamer were subjected to high shear mixing for 50 minutes to obtain Part A.
[0027] Before use, heat the obtained part A to 100-160°C, mix according to the mass ratio of part A and part B to be cured at 3.5:1, stir evenly at >120°C, and keep it for 6 hours to cure to obtain high-performance epoxy Asphalt pavement material. The obtained high-per...
Embodiment 2
[0029] Material:
[0030] Part A: 300 parts of asphalt (Shell AH-70), 80 parts of modified oleic acid, 100 parts of modified ricinoleic acid, 4 parts of benzylamine, 4 parts of a copolymer of ethylene oxide and propylene oxide.
[0031] Part B: Bisphenol A type epoxy resin.
[0032] Preparation:
[0033] Heat the asphalt to 100-130°C, add modified oleic acid and modified ricinoleic acid into the asphalt, stir and mix, then transfer to a colloid mill for high-speed shearing to disperse evenly, the shearing mixing time is 25 minutes, and then add Benzylamine as an accelerator and a copolymer of ethylene oxide and propylene oxide as a defoamer were subjected to high shear mixing for 40 minutes to obtain Part A.
[0034] Before use, heat the obtained part A to 100-160°C, mix according to the mass ratio of part A and part B to be cured at 2.5:1, stir evenly at >120°C, and keep it for 6 hours to cure to obtain high-performance epoxy Asphalt pavement material. The obtained high-p...
Embodiment 3
[0036] Material:
[0037] Part A: 400 parts of asphalt (Zhonghai No. 36-1, No. AH-50), 30 parts of modified oleic acid, 200 parts of modified ricinoleic acid, 4 parts of KOH (produced by Nanjing Chemical Reagent Factory), ethylene oxide and Propylene oxide copolymer 4 parts.
[0038] Part B: Bisphenol A type epoxy resin.
[0039] Preparation:
[0040] Heat the asphalt to 100-130°C, add modified oleic acid and modified ricinoleic acid into the asphalt, stir and mix, then transfer to a colloid mill for high-speed shearing to disperse evenly, the shearing mixing time is 20 minutes, and then add Part A was obtained by high shear mixing of KOH as accelerator and copolymer of ethylene oxide and propylene oxide as defoamer for 40 minutes.
[0041] Before use, heat the obtained part A to 100-160°C, mix according to the mass ratio of part A and part B to be cured at 3.5:1, stir evenly at >120°C, and keep it for 4-8 hours to cure to obtain high performance Epoxy asphalt pavement mat...
PUM
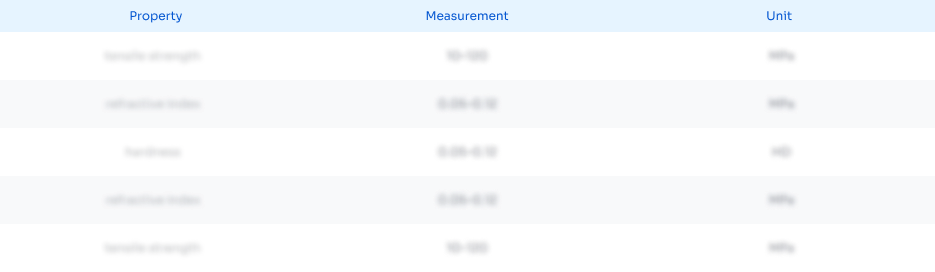
Abstract
Description
Claims
Application Information

- R&D
- Intellectual Property
- Life Sciences
- Materials
- Tech Scout
- Unparalleled Data Quality
- Higher Quality Content
- 60% Fewer Hallucinations
Browse by: Latest US Patents, China's latest patents, Technical Efficacy Thesaurus, Application Domain, Technology Topic, Popular Technical Reports.
© 2025 PatSnap. All rights reserved.Legal|Privacy policy|Modern Slavery Act Transparency Statement|Sitemap|About US| Contact US: help@patsnap.com