Tin-zinc alloy electroplating method
A zinc alloy and plating solution technology, applied in electrolytic components, electrolytic process, cells, etc., can solve problems such as difficulties in the practical application of high-speed electroplating, yellowing, and damage to the plating characteristics of tin-zinc alloys
- Summary
- Abstract
- Description
- Claims
- Application Information
AI Technical Summary
Problems solved by technology
Method used
Examples
Embodiment 1
[0030] After the pretreatment of the steel sheet, electroplating treatment was performed using the following plating bath under conditions of a plating bath temperature of 60° C. and a stirring speed of the plating solution of 50 m / min.
[0031] Stannous sulfate (calculated as tin) 30g / L
[0032] Zinc sulfate (calculated as zinc) 25g / L
[0033] Citric acid 150g / L (0.71mol / L)
[0034] Ammonium sulfate 100g / L
[0035] 1 mole of ethylenediamine and 1 mole of malonate 10ml / L
[0036] The methyl ester was reacted at 85°C for 60 minutes to obtain
[0037] product, so that 1 part of the product and
[0038] 0.5 parts of phthalic anhydride reacted at 95°C
[0039] The product should be obtained in 90 minutes
[0040] pH4 (adjusted with ammonia water)
Embodiment 2
[0042] After the steel plate is pretreated, add 5g / L Nymin NAG-1001 manufactured by NOF (KK) as a nonionic surfactant in the plating bath of Example 1, at a temperature of the plating bath of 60°C, stirring of the plating solution The electroplating treatment was carried out at a speed of 30 m / min.
Embodiment 3
[0044] After the pretreatment of the steel sheet, electroplating treatment was performed using the following plating bath under conditions of a plating bath temperature of 60° C. and a stirring speed of the plating solution of 30 m / min.
[0045] Potassium stannate (calculated as tin) 55g / L
[0046] Zinc oxide (calculated as zinc) 5g / L
[0047] Potassium hydroxide 80g / L
[0048] Potassium carbonate 100g / L
[0049] 1 mole of 1-methylimidazole and 1 mole of benzyl 1g / L
[0050] Chlorine is produced by reacting at 85°C for 180 minutes
[0051] product
[0052] 1 mole of diethylenetriamine and 1 mole of 2-chloroethane 1g / L
[0053] Alcohol reacted at 100°C for 90 minutes
[0054] product
[0055] pH14
PUM
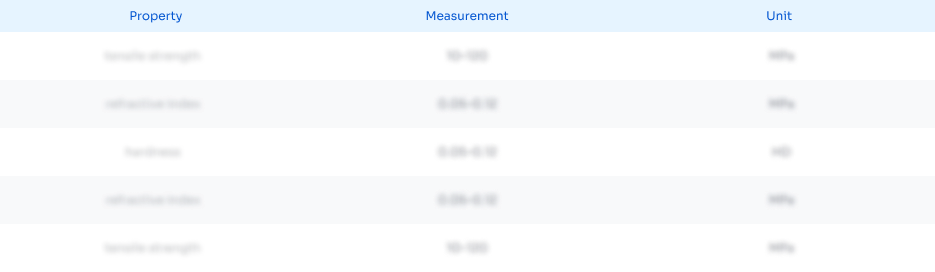
Abstract
Description
Claims
Application Information

- Generate Ideas
- Intellectual Property
- Life Sciences
- Materials
- Tech Scout
- Unparalleled Data Quality
- Higher Quality Content
- 60% Fewer Hallucinations
Browse by: Latest US Patents, China's latest patents, Technical Efficacy Thesaurus, Application Domain, Technology Topic, Popular Technical Reports.
© 2025 PatSnap. All rights reserved.Legal|Privacy policy|Modern Slavery Act Transparency Statement|Sitemap|About US| Contact US: help@patsnap.com