Medium carbon steel on-line balling rolling tech.
A process, carbon steel technology, applied in the field of medium carbon steel online spheroidizing rolling process, to achieve the effect of saving energy, reducing environmental pollution and reducing manufacturing costs
- Summary
- Abstract
- Description
- Claims
- Application Information
AI Technical Summary
Problems solved by technology
Method used
Image
Examples
specific Embodiment approach
[0020] Medium-carbon steel billets with a carbon content of 0.25% to 0.55% are used as raw materials, and conventional methods are used on plate, wire, and bar rolling mills to form rough rolling, intermediate rolling, pre-finishing rolling, and finishing rolling. The rolling temperature of rolling, intermediate rolling and pre-finishing rolling is 900-1050°C. The controlled-rolling-controlled-cooling low-temperature rolling process is adopted in the finishing rolling process, and the rolling temperature is controlled at 680-850°C. It is required that the low-temperature rolling has enough Large deformation, the deformation of the cross-section is 50% to 80% of the cumulative area reduction rate, and the deformation induces the dynamic phase transformation of ferrite, that is, the austenite precipitates ferrite during the deformation process, on the one hand, it increases the ferrite in the structure. Ratio, refine ferrite grains, on the other hand, increase the carbon concentr...
Embodiment 1
[0025] Use any medium-carbon steel billet with a carbon content of 0.25% to 0.55%, the rolling temperature for rough rolling, intermediate rolling, and pre-finishing rolling is 950°C, the metallographic structure of the rolled piece is austenite, and cool to 700°C , rolling deformation at 50% area reduction rate, deformation rate 20 / s, and then cooling to 680°C at 5°C / s, after isothermal process or slow cooling process, the metallographic structure of the rolled piece after natural cooling to room temperature is ferrite Body + carbide spheroidized pearlite.
[0026] The isothermal process is cooling to 680°C and the holding time is 600 seconds; the slow cooling process is cooling to 680°C and then slow cooling at a cooling rate of 0.2°C / s.
Embodiment 2
[0028] Use any medium-carbon steel billet with a carbon content of 0.25% to 0.55%. The rolling temperature for rough rolling, intermediate rolling, and pre-finishing rolling is 950°C. The metallographic structure of the rolled piece is austenite, and it is cooled to 750°C. , rolling deformation at 70% area reduction rate, deformation rate 20 / s, and then cooling to 680°C at 8°C / s, after isothermal process or slow cooling process, the metallographic structure of the rolled piece after natural cooling to room temperature is ferrite Body + carbide spheroidized pearlite.
[0029] The isothermal process is cooling to 680°C and the holding time is 900 seconds; the slow cooling process is cooling to 680°C and then slow cooling at a cooling rate of 0.1°C / s.
PUM
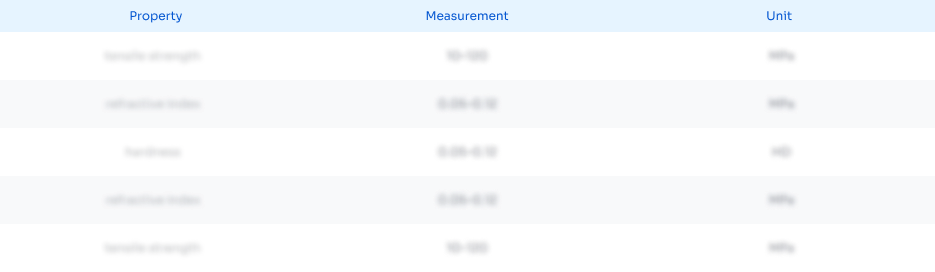
Abstract
Description
Claims
Application Information

- R&D
- Intellectual Property
- Life Sciences
- Materials
- Tech Scout
- Unparalleled Data Quality
- Higher Quality Content
- 60% Fewer Hallucinations
Browse by: Latest US Patents, China's latest patents, Technical Efficacy Thesaurus, Application Domain, Technology Topic, Popular Technical Reports.
© 2025 PatSnap. All rights reserved.Legal|Privacy policy|Modern Slavery Act Transparency Statement|Sitemap|About US| Contact US: help@patsnap.com