Water heat electrophoresis deposition method of gradient iridium silicate coating layer
A technology of electrophoretic deposition and yttrium silicate, which is applied in the field of preparation of yttrium silicate coating, can solve the problems of difficult to meet the requirements of compactness, substrate damage, difficult control of coating uniformity, etc., and achieve thermal damage and oxidation weight loss less than , Excellent anti-oxidation performance
- Summary
- Abstract
- Description
- Claims
- Application Information
AI Technical Summary
Problems solved by technology
Method used
Examples
Embodiment 1
[0038] Embodiment 1: step one: the synthesis of yttrium silicate superfine powder
[0039] 1. Y 4 Si 3 o 12 Synthesis of Ultrafine Powder
[0040] 1.1 According to the molar ratio of Y:Si=2:3, mix 1.25mol / L yttrium nitrate aqueous solution and 1.87mol / L sodium silicate aqueous solution in the same container; mechanically stir at 1000r / min for 10min and place in 100W Oscillate in an ultrasonic container for 10 minutes;
[0041] 1.2 Take the same amount of 1.25mol / L yttrium nitrate aqueous solution and 3.75mol / L sodium hydroxide aqueous solution as in 1.1 and mix them in the same container at a molar ratio of 1:3, and then mechanically stir at 1000r / min for 10min. Place in a 100W ultrasonic container and vibrate for 10 minutes;
[0042] 1.3 Mix the above 1.1 and 1.2 liquid with precipitation in the same container, mechanically stir at 1000r / min for 10 minutes, then place in a 100W ultrasonic container for 10 minutes, filter after shaking, wash the precipitate with distilled...
Embodiment 2
[0071] Step 1: Synthesis of Yttrium Silicate Ultrafine Powder
[0072] 1. Y 4 Si 3 o 12 Synthesis of Ultrafine Powder
[0073] 1.1 According to the molar ratio of Y:Si=2:3, mix 1.25mol / L yttrium nitrate aqueous solution and 1.87mol / L sodium silicate aqueous solution in the same container; mechanically stir at 2000r / min for 30min and place in a 500W Oscillate in an ultrasonic container for 60 minutes;
[0074] 1.2 Take the same amount of 1.25mol / L yttrium nitrate aqueous solution and 3.75mol / L sodium hydroxide aqueous solution as in 1.1 and mix them in the same container at a molar ratio of 1:3, and then mechanically stir at 2000r / min for 30min. Place in a 500W ultrasonic container and vibrate for 60 minutes;
[0075] 1.3 Mix the above 1.1 and 1.2 liquid with precipitation in the same container, mechanically stir at 2000r / min for 90 minutes, then place in a 500W ultrasonic container for 60 minutes, filter after shaking, wash the precipitate with distilled water for 5 times...
Embodiment 3
[0104] Step 1: Synthesis of Yttrium Silicate Ultrafine Powder
[0105] 1. Y 4 Si 3 o 12 Synthesis of Ultrafine Powder
[0106] 1.1 According to the molar ratio of Y:Si=2:3, mix 1.25mol / L yttrium nitrate aqueous solution and 1.87mol / L sodium silicate aqueous solution in the same container; mechanically stir at 1500r / min for 20min and place in a 300W Oscillate in an ultrasonic container for 40 minutes;
[0107] 1.2 Take the same amount of 1.25 mol / L yttrium nitrate aqueous solution and 3.75 mol / L sodium hydroxide aqueous solution as in 1.1 and mix them in the same container at a molar ratio of 1:3, and stir mechanically at 1500r / min for 20min. Place in a 300W ultrasonic container and vibrate for 40 minutes;
[0108] 1.3 Mix the above 1.1 and 1.2 liquid with precipitation in the same container, mechanically stir at 1500r / min for 50 minutes, then place in a 300W ultrasonic container for 30 minutes, filter after shaking, wash the precipitate with distilled water for 4 times P...
PUM
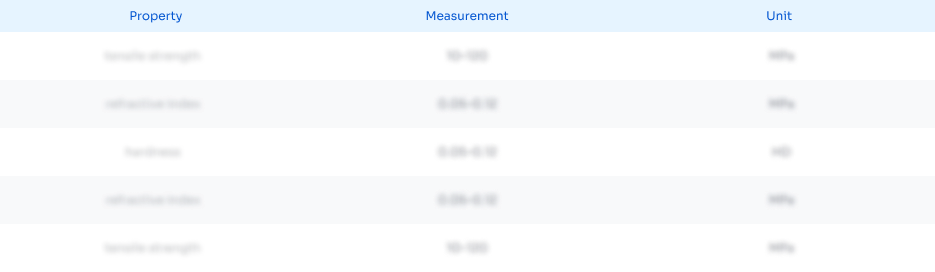
Abstract
Description
Claims
Application Information

- Generate Ideas
- Intellectual Property
- Life Sciences
- Materials
- Tech Scout
- Unparalleled Data Quality
- Higher Quality Content
- 60% Fewer Hallucinations
Browse by: Latest US Patents, China's latest patents, Technical Efficacy Thesaurus, Application Domain, Technology Topic, Popular Technical Reports.
© 2025 PatSnap. All rights reserved.Legal|Privacy policy|Modern Slavery Act Transparency Statement|Sitemap|About US| Contact US: help@patsnap.com