Iron and steel metallurgical compound refining agent
A compound refining agent and iron and steel metallurgy technology, applied in the field of metallurgical refining agents, to achieve the effect of improving kinetics, low equipment investment, and improving mechanical properties
- Summary
- Abstract
- Description
- Claims
- Application Information
AI Technical Summary
Problems solved by technology
Method used
Image
Examples
Embodiment 1
[0027] Embodiment 1: the raw material weight percentage of refining agent:
[0028] CaO 40%, BaO 20%, CaF 2 10%, MgO 10%, NaAIF 6 5%, NaSiF 6 10%, rare earth 5%.
[0029] The preparation process includes:
[0030] (1) Crushing: Use a crusher to break each raw material into 10-30mm particles;
[0031] (2) Mixing: the crushed raw materials are evenly mixed in a ball mill;
[0032] (3) Sieving: use a 100-mesh sieve to sieve the uniformly mixed raw materials, and control the powder particle size at 0.2-2.0mm;
[0033] (4) Drying: Put the sieved raw materials into an oven and bake to remove moisture. The baking temperature is 80-120°C. The baking time is controlled according to the degree of moisture volatilization. Generally, it is based on experience and visual inspection that no water vapor escapes. allow.
[0034] A 2T intermediate frequency induction furnace is used to smelt 200 series stainless steel, the addition amount is 0.8% of the weight of molten steel, and the ...
Embodiment 2
[0040] Embodiment 2: the raw material weight percentage of refining agent:
[0041]CaO 20%, BaO 30%, CaF 2 15%, MgO 17%, NaAIF 6 5%, NaSiF 6 10%, rare earth 3%. The preparation process is the same as in Example 1.
[0042] Use a steel strip with a thickness of 0.35mm to wrap it into a cored wire of ¢10mm. The weight of the core agent is 120g / m. Smelt ordinary carbon steel in a 500Kg intermediate frequency induction furnace. The core wire is fed into the ladle, and the core wire is added according to 0.5% of the weight of the molten steel. The results are shown in Table 2:
[0043] Table 2 Adding refining agent, wire feeding process test results in ladle
[0044]
Embodiment 3
[0045] Embodiment 3: the raw material weight percent of refining agent:
[0046] CaO 40%, BaO 30%, CaF 2 20%, MgO 8%, other 2%.
[0047] (Note: The other 2% can be NaAIF 6 , NaSiF 6 , any combination or single component of the three raw materials of rare earth).
[0048] The preparation process is the same as in Example 1.
[0049] This scheme smelts ordinary carbon steel in a 1T intermediate frequency induction furnace, and the position where the refining agent powder is added is figure 1 Adding position at ladle B, the test results are shown in Table 3:
[0050] Table 3 Adding refining agent test results
[0051]
PUM
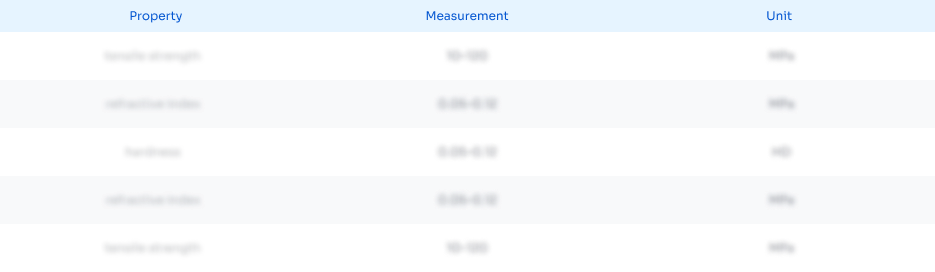
Abstract
Description
Claims
Application Information

- Generate Ideas
- Intellectual Property
- Life Sciences
- Materials
- Tech Scout
- Unparalleled Data Quality
- Higher Quality Content
- 60% Fewer Hallucinations
Browse by: Latest US Patents, China's latest patents, Technical Efficacy Thesaurus, Application Domain, Technology Topic, Popular Technical Reports.
© 2025 PatSnap. All rights reserved.Legal|Privacy policy|Modern Slavery Act Transparency Statement|Sitemap|About US| Contact US: help@patsnap.com