Production of anone by cyclohexane liquid-phase oxidation
A process method, liquid-phase oxidation technology, applied in the direction of chemical instruments and methods, carbon-based compound preparation, organic compound preparation, etc., can solve the problem of reduced selectivity of target products, to avoid further oxidation, good selectivity, avoid The effect of selectivity reduction
- Summary
- Abstract
- Description
- Claims
- Application Information
AI Technical Summary
Problems solved by technology
Method used
Image
Examples
Embodiment 1
[0027] The process flow chart is attached figure 1 , in a reactor 1 with a volume of 30 liters, add 20 liters of cyclohexane, pressurize the whole system to 0.9 MPa with nitrogen, raise the temperature of the reactor to 155°C, and inject Air is introduced to carry out the oxidation reaction, and after the oxidation tail gas passes through the condenser 5 and the gas-liquid separator 6, it is evacuated under the pressure of 0.9 MPa. After reacting for 50 minutes, the mixed solution in the reactor 1 was passed into the high-gravity rotating packed bed 3 with the metering pump 2, and air was passed into the packed bed at the same time, the gas-liquid ratio was 70 (volume under standard conditions): 1, the air It is in parallel contact with the mixed liquid, and the rotor speed of the rotating packed bed is adjusted so that its supergravity level is 60g. After the reaction is completed, the oxidized liquid flows into the product tank 4, and the oxidized tail gas passes through the...
Embodiment 2-6
[0030] The basic steps are the same as in Example 1, the supergravity level of the supergravity reactor is between 15-670g, the air and the mixed solution are in parallel flow contact, and the gas-liquid ratio of the air and the mixed solution is 70 (volume under standard conditions): 1, The result is as follows:
[0031]
Embodiment 7-9
[0033] The basic steps are the same as in Example 1. The supergravity level of the supergravity reactor is 135g, the air and the oxidizing liquid are in parallel contact, and the gas-liquid ratio of the air and the mixed liquor is controlled at 35-100 by adjusting the air flow rate entering the supergravity reactor. (Volume under standard conditions): Varies between 1. The result is as follows:
[0034]
PUM
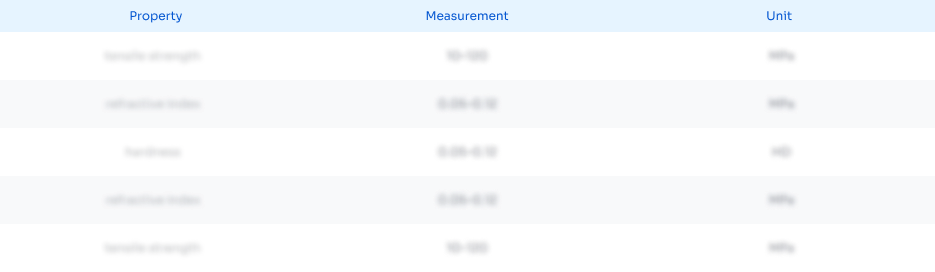
Abstract
Description
Claims
Application Information

- R&D
- Intellectual Property
- Life Sciences
- Materials
- Tech Scout
- Unparalleled Data Quality
- Higher Quality Content
- 60% Fewer Hallucinations
Browse by: Latest US Patents, China's latest patents, Technical Efficacy Thesaurus, Application Domain, Technology Topic, Popular Technical Reports.
© 2025 PatSnap. All rights reserved.Legal|Privacy policy|Modern Slavery Act Transparency Statement|Sitemap|About US| Contact US: help@patsnap.com