Hot press-forging formation mould for magnesium alloy thin shells
A technology for forming molds and magnesium alloys, which is applied to household appliances, manufacturing tools, and other household appliances, etc., to achieve the effect of simplifying the surface treatment process, high mechanical properties, and good surface quality
- Summary
- Abstract
- Description
- Claims
- Application Information
AI Technical Summary
Problems solved by technology
Method used
Image
Examples
Embodiment 1
[0040] The hot stamping and forging forming method of magnesium alloy thin shell parts, the specific process steps are as follows:
[0041] (1) Heat the mold to 200°C;
[0042] (2) Heat the plate with a thickness of 1.5mm to 250°C;
[0043] (3) Evenly smear the blank with lubricant liquid polytetrafluoroethylene;
[0044] (4) Put the blank into the die, and the punch moves downward at a speed of 500mm / s to forge a shell-shaped piece. According to the size and shape of the formed parts, the force applied to the punch is controlled at 5 ton / cm 2 ~15ton / cm 2 .
Embodiment 2
[0046] The hot stamping and forging forming method of magnesium alloy thin shell parts, the specific process steps are as follows:
[0047] (1) Heat the mold to 300°C;
[0048] (2) Heat the plate with a thickness of 3mm to 350°C;
[0049] (3) Spread the lubricant molybdenum disulfide evenly on the billet;
[0050] (4) Put the blank into the die, and the punch moves downward at a speed of 100mm / s to forge a shell-shaped piece. According to the size and shape of the formed parts, the force applied to the punch is controlled at 5 ton / cm 2 ~15ton / cm 2 .
Embodiment 3
[0052] The hot stamping and forging forming method of magnesium alloy thin shell parts, the specific process steps are as follows:
[0053] (1) Heat the mold to 400°C;
[0054] (2) Heat the plate with a thickness of 6mm to 450°C;
[0055] (3) Spread the lubricant graphite evenly on the billet;
[0056] (4) Put the blank into the die, and the punch moves downward at a speed of 10 mm / s to forge a shell-shaped piece. According to the size and shape of the formed parts, the force applied to the punch is controlled at 5 ton / cm 2 ~15ton / cm 2 .
[0057] After punching and forging is finished, the formed part is taken out from the mold, and after cooling, edge trimming is performed to remove excess edges. Then machining, including drilling, cutting and so on. Finally, surface treatment and spraying are carried out to complete the manufacture of finished products.
PUM
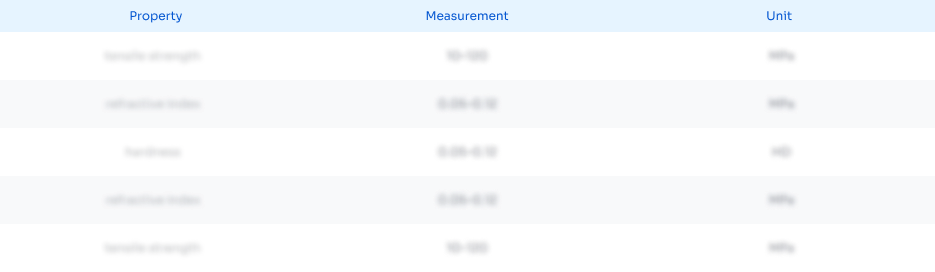
Abstract
Description
Claims
Application Information

- Generate Ideas
- Intellectual Property
- Life Sciences
- Materials
- Tech Scout
- Unparalleled Data Quality
- Higher Quality Content
- 60% Fewer Hallucinations
Browse by: Latest US Patents, China's latest patents, Technical Efficacy Thesaurus, Application Domain, Technology Topic, Popular Technical Reports.
© 2025 PatSnap. All rights reserved.Legal|Privacy policy|Modern Slavery Act Transparency Statement|Sitemap|About US| Contact US: help@patsnap.com